Key Maintenance Metrics Every Facility Manager Should Track
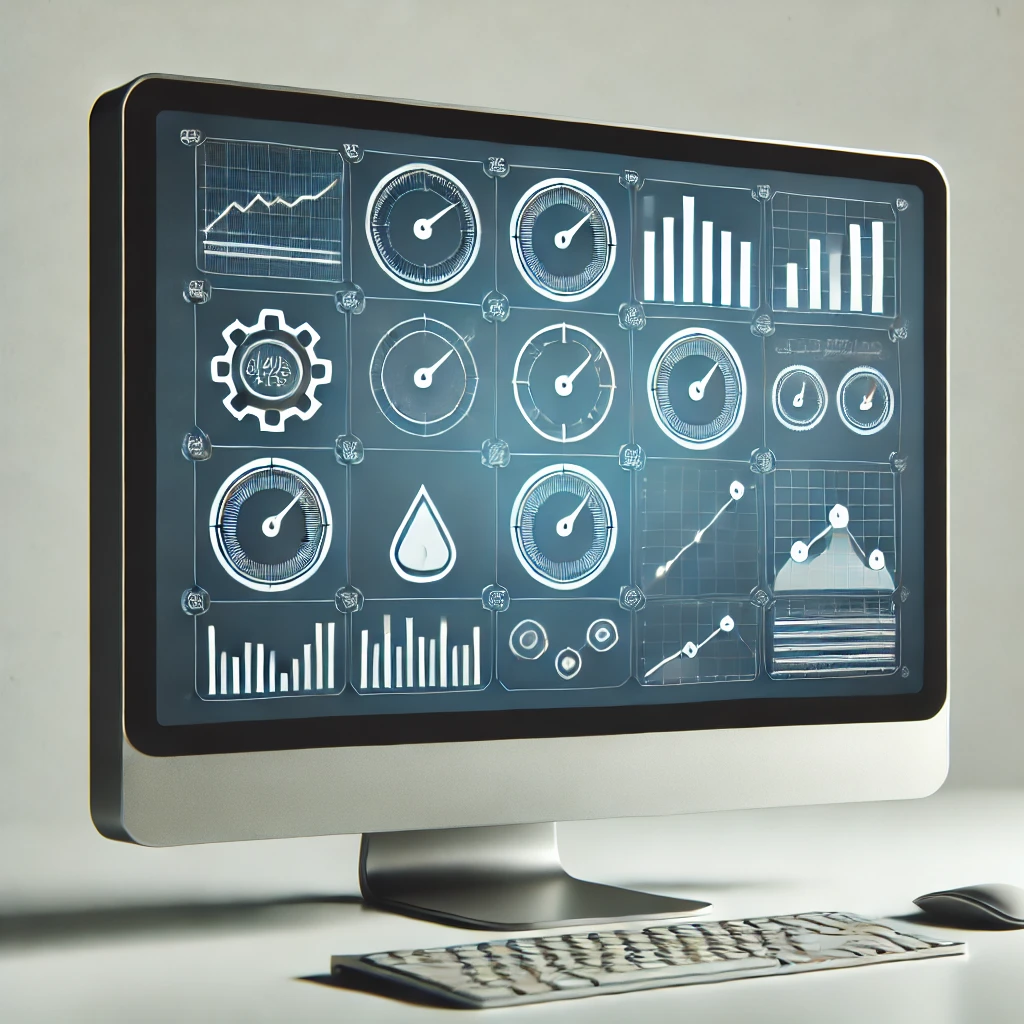
Key Maintenance Metrics Every Facility Manager Should Track
Introduction
Maintenance metrics offer valuable insights into the performance and efficiency of facility operations, enabling managers to make data-driven decisions, improve resource allocation, and optimize maintenance schedules.
By consistently tracking key metrics, facility managers can identify areas for improvement, minimize downtime, and enhance overall facility performance. This guide covers the essential maintenance metrics that every facility manager should monitor to ensure streamlined and effective operations.
For more on measuring facility efficiency and improving maintenance, check out these FlowPath resources:
- Real-Time Analytics and Monitoring with FlowPath CMMS
- Financial Insights with FlowPath
- Equipment Management with FlowPath
Tracking work order completion time is fundamental to understanding how quickly maintenance tasks are addressed. This metric measures the time it takes to complete each work order from creation to resolution. By analyzing work order completion times, facility managers can assess the responsiveness of their maintenance team and identify potential bottlenecks in the workflow. Shorter completion times indicate efficient task handling, while prolonged times may signal issues with resource availability, skill gaps, or process inefficiencies that need to be addressed to enhance response times.
Mean Time to Repair (MTTR) is another critical metric, as it measures the average time required to repair equipment and return it to operational status. MTTR is essential for understanding how long equipment is typically out of service during repairs, providing insights into repair efficiency and equipment reliability. Monitoring MTTR helps facility managers identify which assets experience the most downtime and need closer examination, possibly due to aging components or inadequate preventive maintenance.
In contrast, Mean Time Between Failures (MTBF) measures the average time an asset operates before experiencing a failure. MTBF is a predictive metric, allowing facility managers to evaluate equipment reliability and schedule maintenance proactively to avoid unexpected downtime. A higher MTBF indicates more reliable equipment, while a lower MTBF suggests potential issues that may require additional preventive maintenance or even replacement. By improving MTBF, facility managers can extend the operational life of critical assets and reduce the frequency of disruptive repairs.
Preventive Maintenance (PM) Compliance is a proactive metric that measures adherence to the facility’s preventive maintenance schedule. It tracks whether maintenance tasks are completed on time, as planned, helping to ensure that assets receive regular care and upkeep. High PM compliance rates indicate that a facility is staying on top of its maintenance schedule, reducing the likelihood of equipment failure. Conversely, low compliance can lead to increased downtime and higher reactive maintenance costs, making it an essential metric for facility managers focused on preventive strategies.
Maintenance Backlog represents the volume of work orders that remain open over a specified period, often measured as a percentage of available maintenance hours. A growing backlog may signal insufficient staffing, process inefficiencies, or high equipment failure rates that require further attention. By monitoring backlog levels, facility managers can allocate resources more effectively, prioritize tasks, and ensure that critical work orders are addressed promptly, preventing accumulation that could impact operational efficiency.
Cost per Work Order provides insights into the financial efficiency of maintenance operations by measuring the average cost to complete a maintenance task. This includes labor, materials, and any additional expenses associated with repairs. Tracking this metric allows facility managers to identify cost-saving opportunities, such as sourcing lower-cost parts or implementing training programs to reduce repair times. Lowering the cost per work order can lead to significant savings over time, optimizing the maintenance budget.
Another key metric is Downtime, which quantifies the time an asset is unavailable due to maintenance or repairs. High levels of downtime can negatively impact operations, productivity, and, ultimately, revenue. By tracking downtime, facility managers can determine which assets require more frequent maintenance and prioritize those in critical areas. This metric is essential for optimizing asset availability and maintaining efficient operations.
Lastly, Schedule Compliance measures the percentage of planned maintenance tasks completed on schedule. High schedule compliance indicates that the facility is managing its maintenance tasks efficiently, reducing the need for reactive maintenance. This metric ensures that the facility’s maintenance program is proactive and structured, contributing to smoother day-to-day operations and reduced emergency repairs.
Conclusion
Monitoring these key maintenance metrics enables facility managers to make data-informed decisions, optimize maintenance schedules, and enhance asset performance. Consistently tracking these metrics not only improves operational efficiency but also reduces costs, supports preventive strategies, and maximizes the value of facility assets. For more insights on using technology to enhance facility management, check out our guide on Real-Time Analytics with FlowPath CMMS.
Interested in simplifying your facility’s maintenance tracking? Schedule a Demo with FlowPath today to see how our CMMS can help you monitor and manage maintenance metrics effectively.