Streamline Seasonal Maintenance Planning for Your Facility
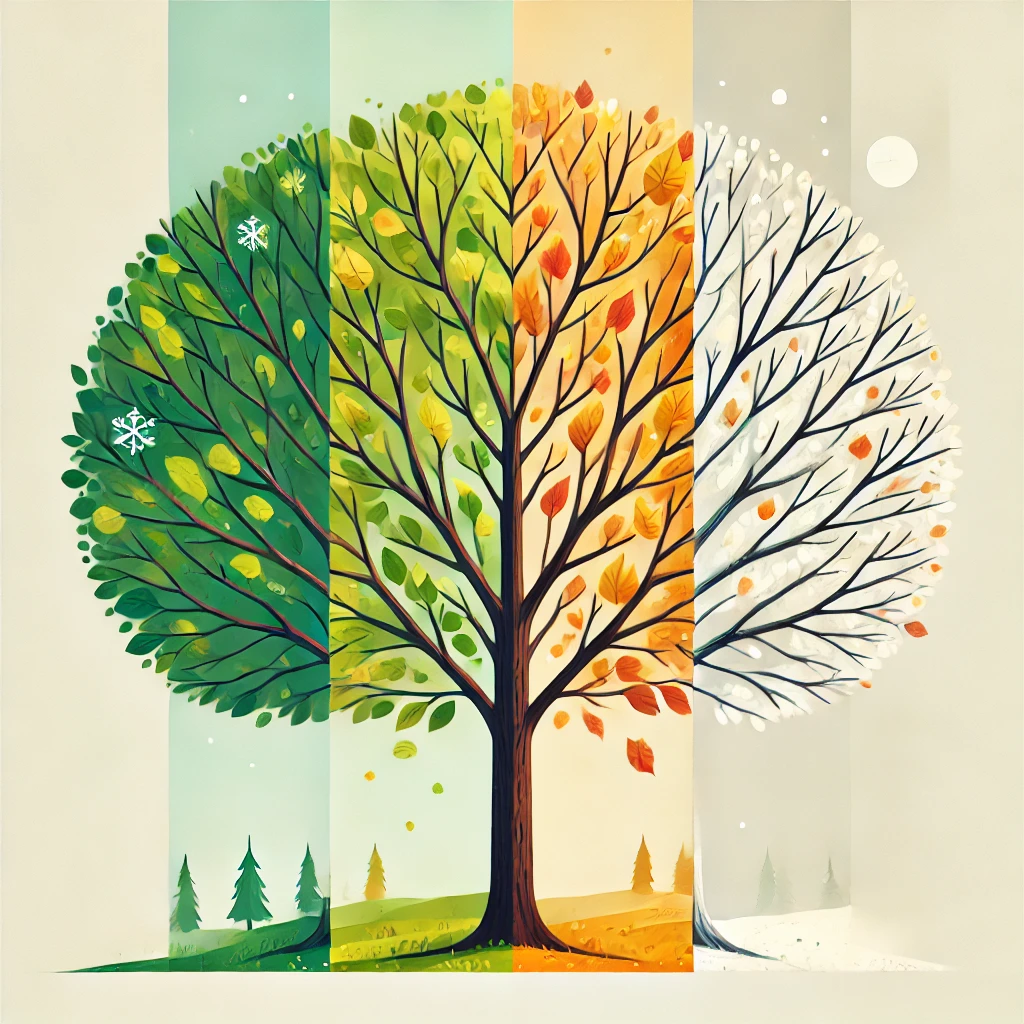
Streamline Seasonal Maintenance Planning for Your Facility
Seasonal maintenance is an essential aspect of facility management that ensures the smooth operation of buildings and equipment throughout the year. By proactively addressing the unique challenges posed by each season, facility managers can minimize downtime, extend asset life, and create a safe, comfortable environment for occupants.
Effective seasonal maintenance planning involves a systematic approach that takes into account the specific needs of each facility, as well as the resources available to address them. This process can be complex and time-consuming, especially for larger organizations with multiple sites and diverse assets.
Fortunately, advances in technology have made it easier than ever to streamline seasonal maintenance planning and execution. By leveraging powerful scheduling tools and automation capabilities, facility managers can optimize their maintenance workflows, reduce manual effort, and ensure that critical tasks are completed on time, every time.
What is Seasonal Maintenance Planning?
Seasonal maintenance planning is the process of identifying, scheduling, and executing maintenance tasks that are specific to each season. This proactive approach ensures that facilities are prepared for the unique challenges posed by changing weather conditions, occupancy levels, and other seasonal factors.
Effective seasonal maintenance planning involves:
- Assessing facility needs: Evaluating the unique requirements of each building, system, and asset based on factors such as age, condition, and criticality.
- Developing a comprehensive checklist: Creating a detailed list of tasks that need to be performed in each season, such as HVAC tune-ups in spring, roof inspections in fall, and snow removal in winter.
- Allocating resources: Ensuring that the necessary personnel, equipment, and materials are available to complete each task efficiently and effectively.
- Scheduling tasks: Assigning specific dates and times for each maintenance activity, taking into account factors such as weather forecasts, occupancy levels, and production schedules.
- Monitoring and adjusting: Regularly reviewing the maintenance plan and making adjustments as needed based on changing conditions or unexpected events.
By following these steps, facility managers can develop a robust seasonal maintenance plan that helps to minimize downtime, extend asset life, and ensure the safety and comfort of building occupants.
One of the key benefits of seasonal maintenance planning is that it allows facility managers to take a proactive approach to maintenance, rather than simply reacting to problems as they arise. By identifying potential issues before they occur and taking steps to prevent them, facility managers can avoid costly repairs, extend the life of their assets, and minimize disruption to building operations.
For example, by scheduling regular HVAC maintenance in the spring and fall, facility managers can ensure that their systems are operating at peak efficiency during the hottest and coldest months of the year. This not only helps to reduce energy costs but also improves indoor air quality and comfort for building occupants.
Similarly, by performing regular roof inspections and repairs in the fall, facility managers can identify and address potential leaks or damage before they lead to more serious problems during the winter months. This can help to prevent costly water damage, mold growth, and other issues that can impact building safety and occupant health.
However, developing and executing a comprehensive seasonal maintenance plan can be a complex and time-consuming process, particularly for larger organizations with multiple sites and diverse assets. This is where technology solutions, such as the scheduling tools offered by Flowpath, can play a critical role in streamlining the process and improving efficiency.
How to Streamline Seasonal Maintenance Planning
Streamlining seasonal maintenance planning requires a strategic approach that embraces technology to automate and optimize scheduling. Implementing advanced tools can significantly enhance the efficiency of maintenance tasks by automating complex processes and ensuring timely completion. This not only reduces the burden on facility managers but also ensures that critical maintenance tasks are never overlooked.
Develop a Seasonal Maintenance Checklist
Crafting a tailored checklist for each season is essential for effective maintenance planning. This list should address specific tasks relevant to seasonal changes, such as inspecting heating systems before winter sets in or preparing irrigation systems for spring. Ensuring that all necessary actions are documented helps maintain a proactive stance in facility management, allowing teams to execute their duties with precision and confidence.
Utilize Scheduling Tools for Efficiency
Employing scheduling software can revolutionize the management of maintenance operations. These tools facilitate the seamless allocation of tasks to team members based on their expertise and current workload. Furthermore, they offer dynamic rescheduling capabilities to adapt to sudden changes, ensuring that disruptions are minimized. By enhancing the coordination of resources, these tools help maintain a streamlined workflow that boosts productivity across the board.
Implement Preventive Maintenance Planning
Incorporating preventive strategies is vital for addressing potential facility issues before they arise. By leveraging historical data and trends, facility managers can schedule maintenance activities that target high-risk areas, thereby preventing costly breakdowns. This approach not only ensures the longevity of assets but also enhances overall operational resilience, focusing efforts where they are most needed.
Leverage Facility Management Tools
Integrating comprehensive management platforms can centralize maintenance operations, improving communication and transparency. These systems enable real-time updates and status tracking, providing a holistic view of ongoing activities. This centralized approach fosters a collaborative environment, promoting efficiency and accountability across all levels of the maintenance team.
Automate Work Orders for Seasonal Tasks
Streamlining work order processes through automation reduces the need for manual oversight and ensures uniformity in task execution. Automating the initiation and routing of work orders guarantees timely action on seasonal tasks, freeing managers to devote their attention to strategic improvements. This efficient handling of routine operations is instrumental in maintaining a responsive and agile maintenance strategy.
1. Develop a Seasonal Maintenance Checklist
Creating a structured approach to seasonal maintenance is crucial for ensuring that your facility remains resilient through the changing conditions of each season. This checklist acts as a strategic guide, specifying the maintenance actions necessary to uphold operational standards and avert potential disruptions. By clearly designating tasks and timelines, facility managers can cultivate a maintenance strategy that anticipates challenges and effectively addresses them.
To devise an effective checklist, start by pinpointing essential maintenance priorities that align with seasonal shifts. For example, during the colder months, focus on tasks like optimizing insulation and ensuring the integrity of weather seals to maintain energy efficiency. As temperatures rise, shift attention to calibrating cooling systems and preparing landscape irrigation for increased usage. Each task should be precise, actionable, and contribute to the overall maintenance objectives of the facility.
Incorporating supplementary activities that address broader maintenance requirements is also vital. Regular evaluation of exterior paintwork, for instance, can prevent weather-related deterioration and preserve the facility’s appearance. Likewise, scheduling checks on drainage systems can mitigate the risk of water accumulation and potential structural damage. By integrating both primary and ancillary tasks, the checklist provides a comprehensive approach, facilitating smooth transitions between seasons.
2. Utilize Scheduling Tools for Efficiency
Integrating sophisticated scheduling solutions into your maintenance operations can significantly boost the effectiveness of task coordination and personnel management. These advanced systems intelligently allocate maintenance activities, ensuring that each task is assigned to the most capable team members based on their expertise and current workload. This ensures that personnel are deployed strategically, minimizing idle time and maximizing productivity across the maintenance team.
These systems offer the ability to swiftly adapt to changing conditions, such as unexpected maintenance demands or shifts in staff availability. By enabling rapid reassignment of tasks and immediate communication with relevant team members, scheduling tools support a nimble maintenance operation that can swiftly respond to any changes. This adaptability is crucial for maintaining seamless operations despite the unpredictable nature of maintenance environments.
Moreover, these tools provide a comprehensive overview of maintenance activities, enabling managers to monitor progress and resource distribution efficiently. By utilizing detailed analytics and insights, facility managers can continuously refine their strategies, identifying areas for improvement and ensuring that maintenance objectives are met with precision. This data-driven approach not only optimizes current processes but also paves the way for more informed, strategic planning in the future.
3. Implement Preventive Maintenance Planning
A forward-thinking approach to facility management involves focusing on predictive maintenance strategies. By anticipating and addressing maintenance needs before they escalate, facilities can maintain operational continuity and safeguard against unexpected disruptions. This methodology not only ensures the smooth functioning of equipment but also optimizes resource allocation, leading to a more resilient infrastructure.
Leveraging advanced analytical tools enables facility managers to forecast maintenance requirements with greater accuracy. By assessing operational data and identifying early warning signs, managers can schedule interventions that preemptively resolve issues. This data-driven approach enhances decision-making processes, allowing for targeted maintenance activities that align with strategic objectives and improve overall facility performance.
Establishing a structured preventive maintenance plan involves setting measurable targets and continuously evaluating outcomes to refine processes. Regular assessments and feedback loops ensure that maintenance efforts remain aligned with organizational goals and adapt to evolving operational demands. This dynamic framework supports a culture of ongoing improvement, fostering an environment where innovation and efficiency thrive.
4. Leverage Facility Management Tools
Facility management tools offer a strategic advantage by integrating various aspects of maintenance operations into a cohesive system. These tools function as the nerve center for maintenance activities, allowing for streamlined operations and enhanced coordination. By uniting maintenance components under a single framework, facility managers can ensure that tasks, resources, and updates are easily accessible and managed efficiently.
Features within these tools, such as automated notifications, play a crucial role in keeping maintenance teams on track with their schedules. These notifications serve as prompts for upcoming tasks, reducing the risk of missing critical deadlines and promoting a disciplined approach to maintenance. Additionally, the ability to track task progress in real-time provides managers with the necessary visibility to make timely adjustments and optimize resource deployment, ensuring that maintenance operations remain efficient and responsive.
The analytical capabilities of facility management tools allow for a thorough examination of maintenance performance, empowering managers to make data-driven decisions. By dissecting performance metrics, managers can uncover trends and areas that require attention, facilitating targeted improvements in maintenance strategies. This analytical approach not only enhances current operations but also supports a proactive maintenance culture, driving continuous improvement and adaptability to meet the evolving demands of the facility.
5. Automate Work Orders for Seasonal Tasks
Leveraging automation in work order processes revolutionizes the handling of seasonal maintenance tasks, eliminating the need for manual entries and promoting efficiency. By automating the initiation and distribution of work orders, facilities can ensure that essential seasonal tasks are tackled promptly and consistently. This approach not only alleviates the administrative workload on staff but also enhances reliability, leading to a more seamless maintenance operation.
Advanced automation tools provide comprehensive oversight of task status, offering facility managers the ability to efficiently track progress and resource allocation. This level of transparency is instrumental in quickly identifying and resolving any inefficiencies or delays, ensuring that maintenance operations proceed without interruptions. Automated notifications keep teams informed about pending tasks and deadlines, reinforcing the importance of timely task completion and adherence to seasonal schedules.
Incorporating predictive analytics with automated work order systems transforms maintenance strategies into proactive initiatives, allowing facilities to prioritize tasks based on urgency and potential impact. This strategic management of maintenance activities not only optimizes resource deployment but also strengthens the resilience and durability of facility assets, ensuring long-term operational success.
6. Best Practices for Maintenance Scheduling
Crafting an effective maintenance schedule demands a strategy that embraces flexibility and regular assessment. By consistently evaluating and refining schedules, facility managers can ensure alignment with facility demands and anticipate future needs. This proactive stance enables managers to swiftly adapt to changes, efficiently allocate resources, and sustain high levels of operational performance.
Incorporating diverse perspectives into the planning process strengthens maintenance scheduling efforts. By collaborating with stakeholders, facility managers can ensure that maintenance strategies support broader organizational goals, optimizing the deployment of resources. This inclusive approach promotes a culture of collective ownership and enhances the effectiveness of maintenance initiatives.
Employing advanced analytical tools provides valuable insights that enhance scheduling practices. Facility managers can harness real-time data to discern patterns, gauge the success of maintenance activities, and make strategic adjustments to future schedules. Through these best practices, organizations can cultivate an agile maintenance framework that bolsters long-term operational resilience.
Tips on Streamlining Seasonal Maintenance Planning
1. Regularly Review and Update Your Checklist
Adaptability is key in maintaining an effective seasonal maintenance plan; continuously refining your checklist allows it to evolve alongside your facility's needs. By integrating feedback from previous maintenance cycles and staying informed on new environmental challenges, your checklist remains a dynamic tool. This approach not only augments the relevance of your maintenance tasks but also ensures preparedness for emerging conditions that could impact facility operations.
2. Optimize Resource Allocation
Maximizing resource efficiency involves a strategic assessment of operational demands and available assets. By leveraging predictive analytics and performance metrics, facility managers can deploy resources where they will have the most impact. This precision in resource management reduces redundancy, enhances productivity, and ensures that maintenance teams can meet the facility's needs with agility and effectiveness.
3. Embrace Automation
Automation stands at the forefront of modernizing maintenance strategies. By automating routine processes and incorporating machine learning algorithms, facilities can anticipate maintenance needs and respond proactively. This technological integration not only minimizes manual oversight but also empowers maintenance teams to focus on complex problem-solving and strategic planning, driving operational excellence.
4. Engage Your Team
Cultivating a participative culture is essential for refining maintenance strategies. By actively seeking input from team members, facility managers can harness diverse insights to enhance maintenance plans. This engagement fosters a sense of collective responsibility and aligns the team towards common objectives, resulting in more innovative and effective maintenance solutions.
By embracing these strategies and leveraging cutting-edge tools, you can transform your seasonal maintenance planning into a streamlined, efficient process that drives operational excellence. With the right approach and technology, you can ensure that your facility remains resilient, safe, and comfortable for occupants, no matter what challenges each season brings. If you're ready to take your seasonal maintenance planning to the next level, schedule a demo with us today and discover how our innovative solutions can help you achieve your goals.