What is Idle Time and How Do I Calculate It?
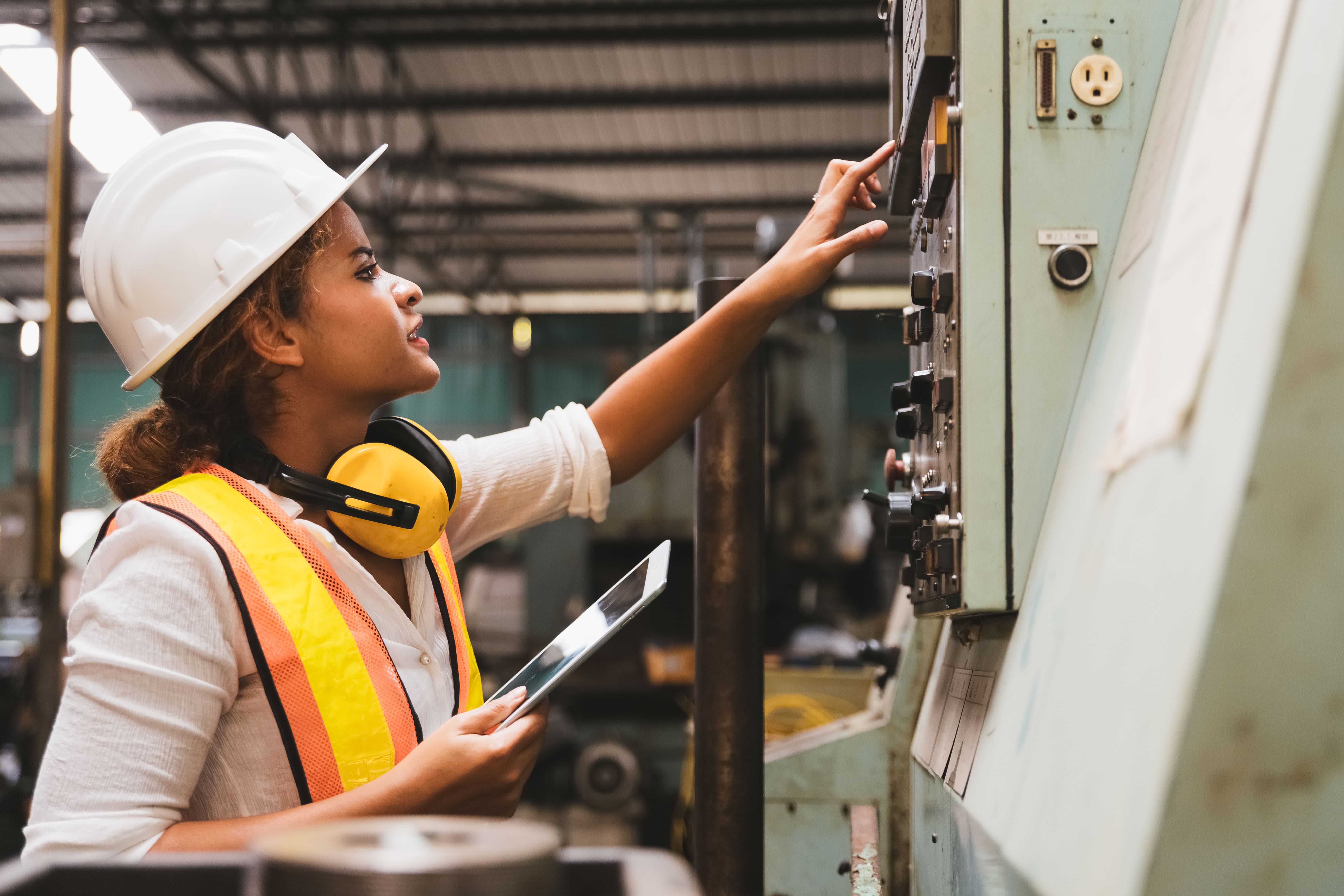
Idle time is a phrase you might hear often in the facility management space, as the term is closely tied to productivity. Reducing idle time allows organizations to devote more time to important tasks and increase the bottom line. But before you can reduce idle time at your facility, it’s important to gain a full understanding of what exactly idle time is and why reducing it can be so beneficial.
What is Idle Time?
Idle time is the period of time when an asset is unproductive, though it is available and ready to work. Also referred to as a “waiting time,” idle time can refer to an asset, machine, or employee, and is typically caused by delays, lack of materials, and workflow inefficiencies.
In these situations, an employee or machine is unproductive due to factors that could be controlled by various factors, such as external partner deliverables or management. For example, idle time may occur because a piece of machinery isn’t working, the company is waiting on a shipment to arrive, or a facility is overstaffed and not everyone being paid to be there has tasks to tend to.
Some level of idle time is inevitable; there is no way to completely mitigate idle time as it’s a natural part of any company with multiple employees and pieces of equipment. But, there are steps you can take to reduce idle time. This is extremely important for any facility because every minute that a machine or employee is idle is a lost minute of productivity, which opens the door to potential revenue loss.
Knowing what factors at your facility can lead to idle time can help you plan ahead so that efficiency and profitability won’t take a big hit.
Types of Idle Time
Understanding the difference between planned and unplanned idle time helps businesses improve operational efficiency, reduce unnecessary downtime, and enhance employee productivity.
Planned Idle Time
Planned idle time, also known as normal idle time, refers to scheduled periods when machines or employees are not engaged in productive activity due to necessary maintenance or planned downtime. This type of idle time is often unavoidable and essential for sustaining long-term efficiency.
Key causes of planned idle time include:
- Preventive maintenance: Routine inspections, servicing, and part replacements that keep equipment running efficiently and prevent unexpected breakdowns.
- Scheduled maintenance tasks: Cleaning, calibration, and testing to ensure compliance with operational and safety standards.
- Employee breaks and shift changes: Time allocated for rest periods or transition between work shifts to maintain worker efficiency.
- Planned downtime for upgrades: Equipment and software updates that improve performance and longevity.
While planned idle time may seem counterproductive, it ultimately contributes to improved efficiency, minimizes costly disruptions, and ensures assets are operating at peak performance.
Unplanned Idle Time
Unplanned idle time, also referred to as abnormal idle time, occurs unexpectedly and leads to inefficiencies in workflow. Unlike planned idle time, it often results in productivity losses, increased costs, and unnecessary delays in completing tasks.
Common causes of unplanned idle time include:
- Equipment failures and emergency maintenance: Unscheduled repairs that disrupt operations and require urgent attention.
- Lack of materials or supplies: Employees or machines waiting due to shortages or delayed deliveries.
- Work order bottlenecks: Poor scheduling or miscommunication leading to waiting time between tasks.
- Inefficient workflows: Gaps in processes that cause unnecessary idle periods and reduce overall efficiency.
Who Tracks Idle Time?
Tracking idle time is essential for improving operational efficiency, reducing costs, and optimizing maintenance schedules. Various roles within an organization are responsible for monitoring and managing idle time to ensure assets and employees are used effectively.
1. Maintenance Managers
Maintenance managers play a key role in tracking idle periods caused by equipment downtime. By leveraging a CMMS, they can monitor maintenance schedules, analyze preventive maintenance effectiveness, and reduce unexpected breakdowns that contribute to unplanned idle time.
2. Facility Managers
Facility managers oversee overall operations and ensure that both assets and employees remain engaged in productive activity. They use time tracking and performance reports to identify inefficiencies, adjust workflows, and schedule planned downtime to minimize disruptions.
3. Operations and Production Managers
In manufacturing and industrial settings, operations managers track idle time to optimize task scheduling, reduce bottlenecks, and improve workflow efficiency. They analyze delays in production lines and implement strategies to minimize waiting time.
4. Technicians and Maintenance Teams
Technicians are responsible for logging idle time due to maintenance activities, including preventive maintenance, repairs, and planned downtime. Their input helps facility teams understand how frequently equipment is unavailable and where efficiency improvements can be made.
5. HR and Workforce Management Teams
Idle time isn't just about machines—it also applies to employees. HR teams track employee productivity by monitoring idle periods during shifts. They use this data to adjust staffing levels, improve task delegation, and reduce excessive downtime in the workforce.
6. Data Analysts and CMMS Software
Modern facilities management technology, such as a CMMS, automates idle time tracking by collecting real-time data on equipment usage, work orders, and maintenance schedules. Data analysts and AI-driven systems help businesses pinpoint inefficiencies, optimize task workflows, and enhance overall efficiency.
By assigning responsibility for idle time tracking across multiple roles, businesses can ensure that both planned and unplanned idle time is managed effectively, leading to improved performance, reduced costs, and greater operational reliability.
Examples of Idle Time
Equipment Stoppages
Lagging equipment can lead to serious operational issues. This could be a result of materials running out, waiting for machines to complete jobs, or power outages. Facility managers should use a CMMS system to develop a proactive maintenance plan in the event that medium to high priority assets experience stoppages.
System Failures
This goes beyond single equipment failures. When an entire system goes down, virtually all employees are left in limbo; work simply cannot be done. This is generally out of the facility’s control, but you can do your best to avoid this by choosing a reliable software system and implementing a troubleshooting process for when common failures occur.
Storms or Other Natural Disasters
Depending on your location and industry, storms or other natural disasters can have huge implications on your day-to-day processes. If you manage a golf course, for example, a rainy day can really hamper the completion of that day’s tasks. The shipping and trucking industry is also largely affected by weather patterns as these aspects play a large role in not only the safety of the trucker and the goods being transported but also the other drivers on the road. Several industries need to take into account and prepare for any idle time that can occur through circumstances that are truly out of our control—like the weather.
Worker Inefficiencies
We’re all human. Avoiding burnout by providing your staff with adequate breaks and time off is vital to the success of your organization. That being said, some employees are inherently more efficient than others. This can be specifically true for new hires who may need an adjustment period. This could also apply to employees who are transitioning roles and/or departments. Poor or unstructured onboarding can also lead to a general lack of understanding among employees. In addition to refining your onboarding process, creating standard operating procedures for different tasks can also keep all employees on the same page.
Unexpected Personal Events
This is an unavoidable type of event that can’t be predicted. When your employees are struggling with things outside of work in their personal lives, it can affect their productivity at work, pushing them to take advantage of the natural idle time of their everyday processes because they’re emotionally exhausted. Simultaneously, large exciting personal life shifts such as employees having to take maternity leave, spend time moving, or take time off to celebrate their wedding are also factors to consider when helping your staff continue seeing success.
The Difference Between Idle Time and Downtime
Though they share similarities, idle time should not be confused with downtime. While in both cases your facility is unproductive, the key difference is in why that could be happening.
When we talk about machine downtime, the problem is usually rooted in either machine failure or scheduled maintenance. While idle time occurs when work could still get done, downtime takes place when work simply can’t be done.
Both of these metrics represent times when your equipment isn’t running, but it’s important to track them separately. Both represent a loss in productivity, but the difference is that idle time can be put to good use.
How to Calculate Idle Time
Idle time can be calculated by taking the difference between the time an asset is scheduled to work and the actual number of productive hours that were spent.
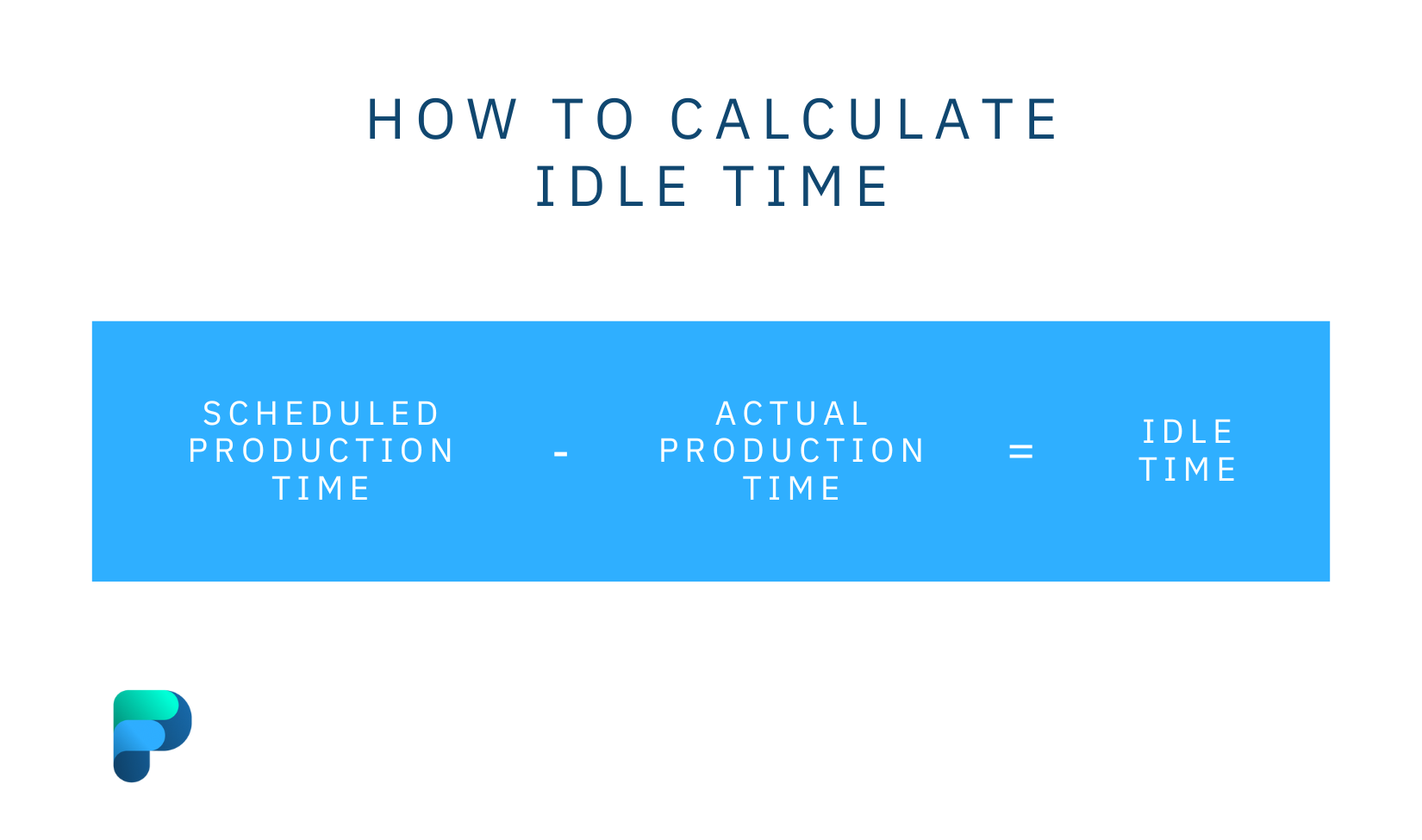
Idle Time = Scheduled Production Time – Actual Production Time
For example, an employee may clock an 8-hour shift, but in their work tracking platform, they may only track 6 hours and 40 minutes of productive work. If they were truly tracking every minute of work performed, this suggests that they had an hour and 20 minutes of idle time. It’s important to note that idle time is not always a negative aspect of an employee’s performance. Time spent on other things that are not on the to-do list could be spent contributing to the facility’s culture or getting to know coworkers, clients, and customers. Considering how idle time could potentially be positive will also be key in determining how much of it to consider eliminating.
Tracking idle time can get a bit more complicated when it comes to machinery since machines often require things like cooldown periods and sometimes cleaning periods. For example, a machine may need to work for 16 hours. That same machine could take 10 minutes to power up, 5 minutes to shut down, and a 30-minute break for cleaning. The machine may also be stopped for 15 minutes during shift changes. In this example, the machine would have one hour of downtime every day.
As we mentioned earlier, you do not necessarily need to reduce your idle time to zero. Employees need breaks. And some tasks, especially manual labor, aren’t so easily tracked. Machinery also typically needs idle time to continue operating effectively. However, actively tracking your idle time will allow you to stay on top of processes that can be streamlined to improve overall productivity.
4 Ways to Manage and Reduce Idle Time
While achieving 100% efficiency is unrealistic, businesses can take strategic steps to minimize idle time and enhance operational efficiency. By identifying idle periods, optimizing workflows, and maintaining assets, organizations can significantly reduce unnecessary downtime.
1. Define and Track Idle Time
The first step in reducing idle time is understanding what it looks like in your facility. Identify and differentiate between planned idle time (such as planned downtime for preventive maintenance) and unplanned idle time caused by equipment failures or waiting time for materials. Implement time tracking systems and establish key performance indicators (KPIs) to pinpoint inefficiencies and areas for improvement.
2. Improve Communication and Task Coordination
Poor communication and unclear scheduling contribute to abnormal idle time by leaving employees uncertain about their tasks. Ensuring teams have real-time access to schedules, work orders, and asset availability minimizes delays. Using a CMMS to automate task assignments, send alerts, and centralize information can improve employee productivity and streamline operations.
3. Prioritize Preventive Maintenance
Equipment breakdowns and maintenance delays are major contributors to unplanned idle time. A preventive maintenance strategy ensures that assets receive regular servicing, reducing unexpected failures and keeping production on track. A CMMS helps schedule, track, and automate maintenance tasks, ensuring critical equipment remains operational while avoiding costly idle periods.
4. Optimize Workflows and Resource Allocation
Reviewing workflows to identify inefficiencies is crucial for maximizing efficiency. Ensure that employees, tools, and materials are available when needed, reducing waiting time and unnecessary delays. Automating task distribution, analyzing asset performance, and leveraging AI-driven maintenance insights can help create a more productive and efficient operation.
By implementing these strategies, businesses can significantly reduce idle time, improve maintenance efficiency, and boost overall operational performance.
Benefits of Tracking Idle Time
Tracking idle time is crucial for improving operational efficiency, reducing unplanned downtime, and maximizing resource utilization. By identifying periods when assets or employees are unproductive, businesses can take proactive steps to minimize delays, optimize workflows, and improve employee productivity. Here are some key benefits of tracking idle time:
1. Improved Operational Efficiency
Monitoring idle time helps organizations pinpoint inefficiencies in workflows and identify the causes of waiting time. By addressing these gaps, businesses can streamline processes, allocate resources more effectively, and improve overall efficiency.
2. Better Preventive Maintenance Scheduling
Tracking idle periods allows facilities to schedule preventive maintenance during planned downtime, reducing disruptions to daily operations. This proactive approach prevents abnormal idle time caused by unexpected breakdowns and extends the lifespan of critical assets.
3. Enhanced Employee Productivity
By analyzing idle time, managers can adjust workloads, improve task delegation, and ensure employees are engaged in productive activities. Reducing unnecessary downtime keeps teams focused and improves overall job performance.
4. Reduced Maintenance Costs
Excessive idle time in equipment often signals underlying maintenance issues. Regular tracking helps businesses detect early warning signs of wear and tear, preventing costly repairs and minimizing the risk of equipment failure.
5. Optimized Asset Utilization
Unused assets represent a loss of potential value. By tracking idle time, organizations can make informed decisions about equipment deployment, ensuring assets are fully utilized rather than sitting dormant.
6. Data-Driven Decision Making
A CMMS (Computerized Maintenance Management System) with time tracking capabilities provides actionable insights into operational performance. Facilities can leverage this data to refine scheduling, enhance task management, and drive continuous improvements in efficiency.
Tracking idle time is essential for businesses looking to maximize operational efficiency, reduce waste, and maintain a proactive approach to maintenance and resource management. By integrating CMMS technology, organizations can seamlessly monitor, analyze, and minimize idle time to boost productivity and lower costs.
Why Choose FlowPath?
Are you optimizing your workflows? Implementing project tracking and reporting can do wonders when it comes to reducing idle time. With an all-in-one software like FlowPath, you can do just that and more. Automate work orders and maintenance, schedule events, and keep your team in the loop with FlowPath’s top-of-the-line facility management software.
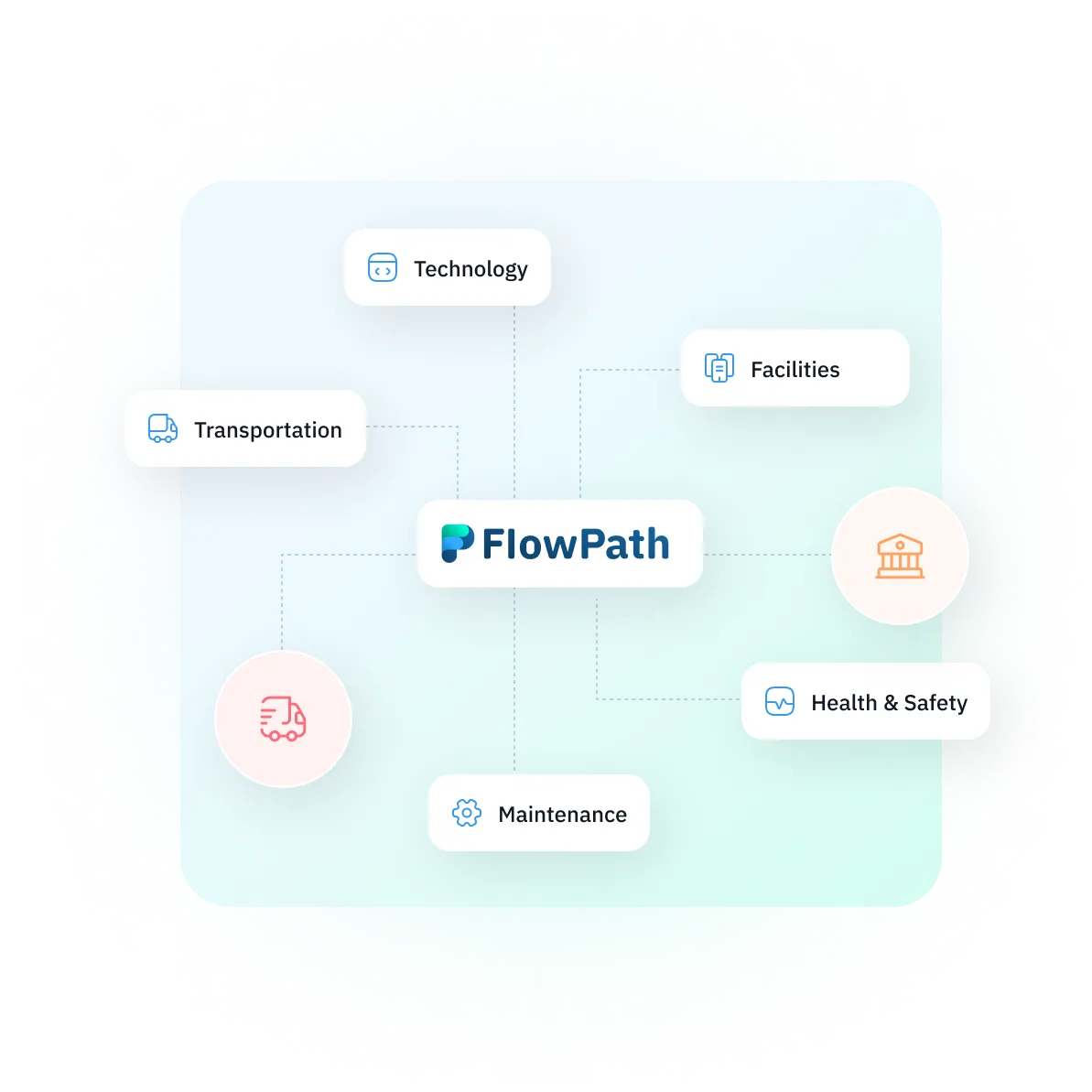
Reduce idle time, within reason, and get ahead of your facility’s operations today. Schedule a demo and see how FlowPath can help reduce your facility’s idle time and make your life easier.
----
FAQs About Idle Time
What is idle time?
Idle time is the amount of time spent waiting to use viable equipment, or nonproductive time by employees caused by unforeseen work stoppages
How do you calculate idle time?
Idle Time = Scheduled Production Time – Actual Production Time
What is the difference between idle time and downtime?
Idle time is time during which an asset is waiting to run or isn’t scheduled to run. Downtime is when an asset is incapable of performing its function, either due to an unplanned outage or planned maintenance. While idle time occurs when work could still get done, downtime takes place when work simply can’t be done.