How to Streamline Your Work Order Management Process
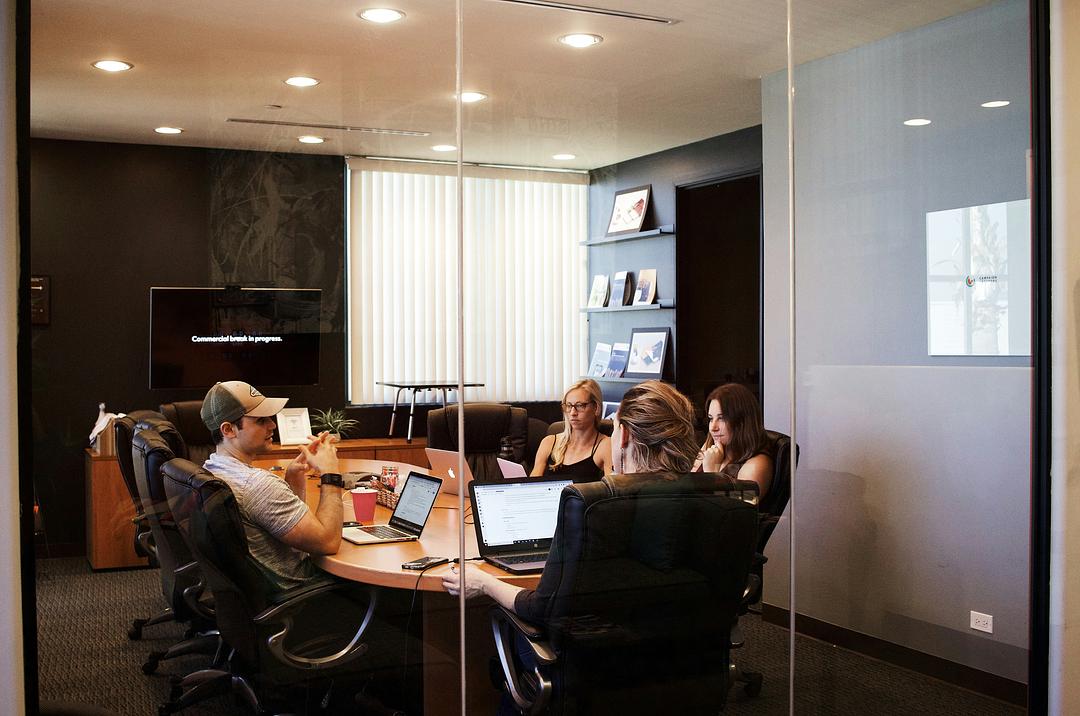
How to Streamline Your Work Order Management Process
Work order management is a critical component of efficient facility operations. When done effectively, it can significantly reduce downtime, minimize delays, and boost overall productivity.
However, managing work orders can be a complex and time-consuming process. It involves coordinating multiple tasks, prioritizing jobs, and ensuring effective communication among team members.
Fortunately, by implementing best practices and leveraging the right tools, organizations can streamline their work order management process. This article will explore what work order management entails and provide actionable strategies to optimize this essential aspect of facility management.
What is Work Order Management?
Work order management is the process of organizing, tracking, and overseeing maintenance and repair tasks from start to finish. It encompasses the entire lifecycle of a work order—from the initial request to the final completion and documentation.
The primary goal of work order management is to ensure that all maintenance tasks are prioritized, assigned, and executed in a timely and efficient manner. By effectively managing work orders, organizations can:
- Reduce equipment downtime
- Increase asset lifespan
- Improve resource allocation
- Enhance communication and collaboration
- Ensure compliance with safety and regulatory standards
In essence, work order management serves as the backbone of a well-functioning maintenance department. It provides a structured approach to handling both planned and unplanned maintenance tasks, enabling teams to work smarter, not harder.
How to Streamline Your Work Order Management Process
Optimizing work order management is key to enhancing workflow efficiency and minimizing disruptions. By adopting a strategic approach and integrating advanced technology, organizations can elevate their work order systems into highly efficient operations. This involves a combination of establishing cohesive systems, setting clear priorities, automating routine tasks, improving information flow, and leveraging real-time insights.
Implement a Cohesive System
A cohesive system acts as the cornerstone for streamlined work order management. By employing comprehensive work order management software, organizations can create a centralized hub for task oversight, ensuring all assignments are easily tracked and coordinated. This system enhances visibility across team members, promotes seamless communication, and supports effective resource distribution. The result is a reduction in oversight and an improvement in collaborative efforts, fostering a more synchronized workflow.
Prioritize Work Orders Wisely
Strategic prioritization is essential for efficient work order management. Establishing a well-defined framework that categorizes tasks based on urgency and significance guarantees that pressing issues receive immediate attention. Factors such as operational continuity, safety, and compliance should guide priority settings. An organized prioritization scheme helps allocate resources judiciously, averting potential bottlenecks and ensuring that critical assignments are promptly addressed.
Automate Routine Tasks
Automation serves as a pivotal element in refining work order management. By automating repetitive activities such as scheduling and notifications, organizations can significantly decrease manual oversights and allocate more time to pressing concerns. Automation tools efficiently manage routine processes, boosting overall productivity and enabling teams to focus on essential tasks. This shift towards automation fosters a proactive environment where potential challenges are preemptively resolved.
Improve Information Flow
Ensuring transparent access to information for all stakeholders is crucial for effective work order management. Establish clear channels that facilitate consistent communication across teams, providing everyone with access to essential data. Comprehensive documentation of each work order phase offers valuable insights for future evaluations and performance assessments. This proactive approach to information flow not only enhances coordination but also aids in tracking progress and pinpointing improvement opportunities.
Leverage Real-Time Insights
Real-time monitoring of work orders is vital for maintaining operational control and meeting deadlines. Implementing systems that provide instantaneous updates allows for swift interventions if tasks fall behind schedule, ensuring minimal disruption and continuity of operations. This active oversight empowers organizations to adapt quickly to changes, guaranteeing the timely completion of work orders. Real-time insights also support data-driven decision-making, enabling managers to refine processes and boost overall efficiency.
1. Implement a Centralized System
Adopting an integrated system for work order management consolidates various processes into a streamlined operation. By utilizing an integrated platform, organizations can ensure comprehensive oversight of all tasks, from initiation to completion. This integration not only enhances task coordination but also significantly reduces the potential for oversight, preventing missed tasks that could lead to costly delays.
Integrated systems facilitate the seamless flow of information, making it readily available to all relevant personnel. This transparency enhances collaboration among team members by ensuring alignment on task status, priorities, and resource distribution. Furthermore, an integrated system offers critical data insights, allowing managers to track performance metrics and identify opportunities for improvement. With all information centralized, leaders can make data-driven decisions that enhance operational efficiency.
The adoption of an integrated system also simplifies the documentation and analysis of work orders. By aggregating data within a single platform, organizations can produce detailed reports that provide a comprehensive view of maintenance activities and outcomes. This capability proves invaluable for compliance and auditing, delivering accurate records of all completed work. Additionally, streamlined reporting facilitates the swift identification of trends and patterns, informing strategic planning and resource management.
2. Prioritize Work Orders Effectively
Setting clear priorities for work orders is essential for maintaining operational fluidity and ensuring that tasks with significant impact are attended to promptly. A comprehensive approach to assigning priorities involves evaluating work orders based on their potential effects on overall operations. This systematic method allows for optimal resource distribution, reducing inefficiencies and enhancing workflow.
Design a Priority Assignment Strategy
Building a priority assignment strategy starts by identifying key factors that influence the urgency of work orders. Consider elements like the critical nature of the task, potential operational disruptions, and alignment with strategic goals. Establishing detailed criteria helps ensure that tasks with the highest impact on business continuity are prioritized effectively, minimizing service interruptions and enhancing efficiency.
Implement a Structured Ranking System
A structured ranking system categorizes work orders into levels that reflect their importance. This system facilitates the quick identification and allocation of resources to tasks that have a direct influence on operational performance. For example, tasks essential to maintaining core functions or preventing significant disruptions should be prioritized more highly than routine activities. This structured ranking ensures that essential issues receive timely resolution, maintaining uninterrupted operations.
- Critical Operational Tasks: Focus on work orders that directly affect core business functions or prevent key disruptions. Addressing these tasks swiftly ensures continued operational performance and minimizes potential setbacks.
- Strategic Impact: Prioritize tasks that align with organizational goals, such as process improvements or efficiency enhancements. These tasks drive long-term success and are crucial for maintaining competitive advantage.
- Routine Preventive Maintenance: Schedule regular maintenance to prevent equipment degradation and sustain asset health. Although not urgent, these tasks are vital for long-term reliability and efficiency.
Regularly Evaluate and Update
Given the dynamic nature of operational environments, it's important to regularly review and refine priority strategies to adapt to new challenges. Continuous evaluation of prioritization practices allows organizations to stay responsive to evolving needs and optimize resource allocation. This proactive stance empowers facility managers to refine their approaches, ensuring alignment with shifting business priorities.
By establishing a strategic priority assignment approach, organizations can manage work orders more effectively, allocate resources efficiently, and support a high-performing operational environment. This targeted strategy not only enhances task execution but also fosters a resilient and forward-thinking organizational culture.
3. Automate Routine Processes
Incorporating automation into work order management processes enhances operational efficiency by streamlining repetitive tasks. By utilizing advanced software solutions, organizations can automate functions such as task scheduling and real-time alerts, significantly reducing the need for manual intervention. This shift towards automation not only minimizes the risk of human error but also allows teams to concentrate on more complex challenges that require their expertise.
Advantages of Leveraging Automation
- Enhanced Precision: Automation ensures a consistent and error-free approach to scheduling and data handling, which is critical for maintaining a reliable work order system. This level of accuracy supports effective decision-making and resource allocation.
- Resource Optimization: With routine tasks managed by automated systems, team members can dedicate more time to high-priority projects, thus optimizing their workload. This reallocation of resources leads to a more agile and responsive maintenance operation.
- Scalability in Operations: Automation provides the ability to manage an increased volume of work orders without additional strain on resources. This scalability is essential for businesses aiming to expand their operations efficiently without compromising service quality.
Implementing Automation Techniques
- Dynamic Task Allocation: Deploy automation to dynamically assign tasks based on real-time data and resource conditions. This approach ensures that work orders are distributed efficiently, enhancing workflow fluidity and resource utilization.
- Instantaneous Alert Systems: Establish automated alert systems to provide immediate updates on task progress and any changes in operational priorities. These real-time notifications keep all stakeholders informed and ready to adapt to new developments swiftly.
- Seamless Data Synchronization: Use automation to integrate data seamlessly across various platforms, providing comprehensive insights into maintenance needs and asset performance. This continuous data flow aids in predictive maintenance and strategic planning, allowing for informed decision-making.
By integrating these automated processes, organizations can transform their work order management, resulting in enhanced efficiency, precision, and scalability. This technological advancement empowers teams to focus on driving critical initiatives and fosters a proactive maintenance culture.
4. Enhance Communication and Documentation
Effective work order management relies on robust communication and precise record-keeping. By implementing streamlined communication strategies, organizations can maintain alignment and ensure that all team members access the necessary information to execute tasks successfully. This involves creating systems that enable seamless interaction, thereby minimizing errors and enhancing coordination.
Establishing Effective Communication Channels
To improve collaboration across teams, organizations should adopt advanced communication technologies that facilitate real-time information exchange. This can include platforms that integrate project management tools with communication features, allowing for efficient task coordination and swift issue resolution. By employing such technologies, teams can ensure that updates are disseminated promptly, supporting a cohesive workflow.
- Integrated Collaboration Platforms: These platforms combine communication and task management, enabling teams to share updates and insights within a unified interface. This integration ensures that everyone remains informed, fostering a culture of responsiveness and adaptability.
- Consistent Information Sharing: Regularly scheduled updates and briefings help maintain clarity regarding project statuses and priorities. These structured communication efforts ensure that all team members are aligned and prepared to address any emerging challenges.
Maintaining Comprehensive Documentation
Accurate documentation is essential for tracking work order progress and informing future strategies. By systematically recording each task's details, organizations can build a comprehensive database that serves as a valuable resource for decision-making and continuous improvement.
- Detailed Task Records: Ensure that every work order entry includes all pertinent information, such as task objectives, responsible personnel, and any deviations encountered. This thorough documentation facilitates accountability and provides a foundation for evaluating performance outcomes.
- Data-Driven Insights: Utilize documented information to conduct detailed analyses of maintenance patterns and performance metrics. These insights can guide strategic planning, enabling organizations to anticipate potential issues and implement proactive solutions.
By refining communication and documentation practices, organizations can cultivate a work environment characterized by transparency and efficiency. This approach empowers teams to execute tasks with precision, driving operational excellence and fostering a culture of continuous improvement.
5. Utilize Real-Time Tracking and Monitoring
Incorporating real-time tracking and monitoring significantly enhances the responsiveness of work order management systems. By employing sophisticated tracking solutions, organizations can instantly assess the status of ongoing tasks, enabling swift adjustments to maintain workflow integrity. This proactive surveillance helps ensure tasks adhere to schedules, reducing the likelihood of delays and maintaining seamless operations.
Advantages of Continuous Tracking
- Instantaneous Oversight: Real-time tracking systems provide immediate updates on work order progress, allowing managers to quickly identify and address any anomalies. This transparency supports agile management, ensuring tasks remain on track and aligned with objectives.
- Strengthened Accountability: Continuous visibility into task progress holds teams accountable by making performance metrics accessible to all stakeholders. This openness promotes responsibility and encourages teams to adhere to established deadlines and quality benchmarks.
- Informed Strategic Planning: The collection of real-time data offers valuable insights that inform strategic planning and resource management. With a clear understanding of ongoing trends and performance metrics, managers can make decisions that align with broader business goals.
Implementing Continuous Monitoring Strategies
- Comprehensive Dashboards: Utilize comprehensive dashboards that consolidate data from various sources, offering a holistic view of work order statuses. These dashboards can be tailored to highlight critical performance indicators, enabling managers to prioritize areas that demand immediate attention.
- Proactive Notifications: Establish proactive notification systems that alert relevant team members to any deviations from expected timelines or changes in task status. These notifications empower teams to quickly address issues, minimizing disruptions and ensuring efficient task completion.
- Seamless System Integration: Employ seamless integration technologies that connect tracking systems with other operational platforms, such as inventory management or scheduling tools. This integration ensures consistent information flow across departments, facilitating coordinated efforts and efficient resource allocation.
By adopting real-time tracking and monitoring, organizations can elevate their work order management processes, fostering an environment of efficiency and adaptability. This capability not only enhances operational oversight but also empowers teams to adapt swiftly, driving progress towards achieving organizational objectives.
Tips on Enhancing Work Order Management
Optimizing work order management involves strategic investments and dynamic process evaluations. By focusing on adaptable systems and continuous improvement, businesses can enhance their operational effectiveness.
1. Invest in a Robust Work Order Management System
Choosing the right work order management system is vital for aligning with company growth. A solution that evolves with your operational demands ensures long-term success. When assessing potential systems, focus on:
- Flexibility: Select a platform that can adjust to increased workload and complexity as your operations scale. This ensures that the system remains efficient and effective over time.
- Intuitive Design: Ensure the system is easy to navigate for all users, from maintenance staff to executive managers. An intuitive design promotes user engagement and reduces training time.
- Integration Potential: Look for systems that can seamlessly connect with your existing technology stack. This capability enhances workflow cohesion and maximizes the utility of your current tools.
- Innovative Functionalities: Consider features like IoT connectivity, AI-driven analytics, and customizable dashboards. These innovations empower teams to optimize maintenance strategies and proactively address emerging challenges.
A well-chosen system not only meets present needs but also prepares the organization for future technological advancements and operational shifts.
2. Regularly Review and Adjust Processes
Ongoing refinement is key to maintaining an effective work order management system. Regular reviews allow organizations to pinpoint inefficiencies and adapt to evolving requirements. Key considerations include:
- Data-Driven Insights: Utilize analytics to track KPIs like task completion rates and resource allocation efficiency. These insights provide a clear picture of where improvements are needed.
- Stakeholder Engagement: Actively seek input from team members and clients to understand the practical impacts of your work order processes. This feedback is crucial for identifying areas of improvement.
- Adaptive Strategies: Be prepared to implement process changes swiftly in response to new data or shifts in business objectives. Agility in strategy ensures that the organization remains resilient and responsive.
- Skill Enhancement: Regularly update training programs to keep personnel informed about new methods and tools. Continuous learning fosters an environment of innovation and adaptability.
By embracing regular evaluations and modifications, organizations can sustain a work order management system that aligns with their strategic goals and industry trends. This proactive stance ensures ongoing operational efficiency and adaptability in a dynamic business landscape.
By implementing these strategies, you can transform your work order management process into a streamlined, efficient operation that drives long-term success. Embracing innovative solutions and fostering a culture of continuous improvement will position your organization at the forefront of the evolving facility management landscape. If you're ready to take your work order management to the next level, schedule a demo with us today and discover how our cutting-edge tools can revolutionize your operations.