Comprehensive HVAC Maintenance Checklist for Facility Managers
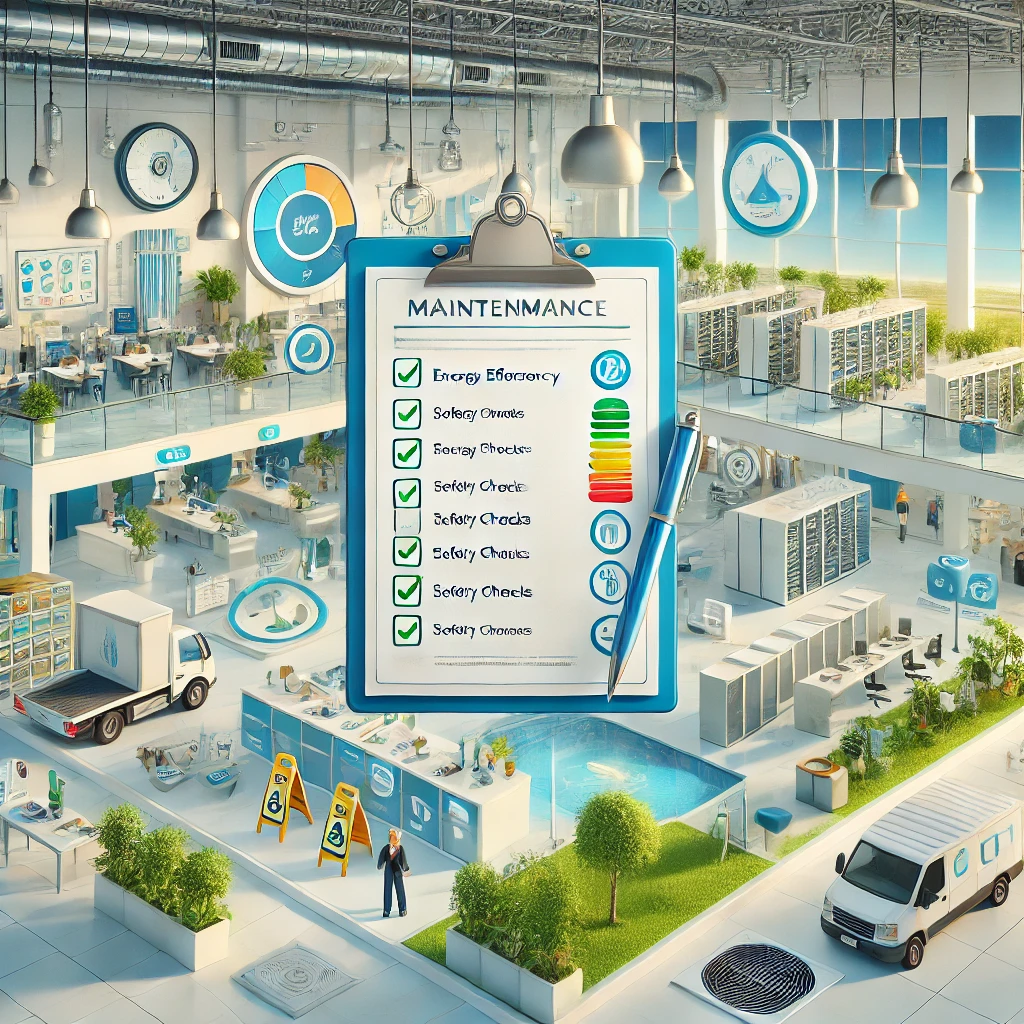
Comprehensive HVAC Maintenance Checklist for Facility Managers
A well-maintained HVAC system is crucial for ensuring a comfortable and safe environment in any facility. Regular maintenance not only optimizes the system's performance but also helps prevent costly breakdowns and extends the equipment's lifespan.
Facility managers and maintenance professionals are tasked with keeping HVAC systems running smoothly, which can be a complex and time-consuming responsibility. To streamline this process and ensure that no critical tasks are overlooked, many turn to HVAC maintenance checklists.
These checklists serve as a comprehensive guide, outlining the essential tasks that need to be performed to keep HVAC systems in top condition. By following a structured maintenance plan, facility managers can proactively address potential issues, improve energy efficiency, and maintain a healthy indoor environment for occupants.
What is an HVAC Maintenance Checklist?
An HVAC maintenance checklist is a detailed, step-by-step guide designed to help facility managers and maintenance teams keep their heating, ventilation, and air conditioning systems running at peak performance. It serves as a roadmap for conducting thorough inspections, identifying potential problems, and performing necessary repairs or adjustments.
The checklist typically covers a wide range of components and tasks, including:
- Filters: Inspecting, cleaning, or replacing air filters regularly to maintain air quality and prevent restricted airflow.
- Electrical Connections: Checking and tightening electrical connections to ensure safe and efficient operation of the system.
- Coils: Cleaning evaporator and condenser coils to maintain proper heat transfer and prevent energy waste.
- Refrigerant Levels: Monitoring refrigerant levels to ensure the system is operating at optimal efficiency.
- Belts and Bearings: Inspecting and replacing worn belts, and lubricating moving parts to minimize friction and prevent premature wear.
- Thermostats and Controls: Testing thermostats and control systems to verify proper operation and maintain desired temperature settings.
By following a comprehensive HVAC maintenance checklist, facility managers can catch minor issues before they escalate into major problems. This proactive approach not only saves time and money in the long run but also helps extend the life of the equipment—a significant benefit considering the substantial investment that HVAC systems represent.
Moreover, regular maintenance guided by a checklist helps ensure compliance with safety regulations and manufacturer recommendations. It provides a clear record of the tasks performed, making it easier to track maintenance history and plan future service.
Implementing an HVAC maintenance checklist, such as those offered by Flowpath's CMMS solution, empowers facility managers to take control of their HVAC systems. By streamlining the maintenance process and providing a structured approach, these checklists enable teams to work more efficiently, reduce downtime, and create a more comfortable, productive environment for building occupants.
How to Use an HVAC Maintenance Checklist
Start by conducting a detailed evaluation of the HVAC components present in your facility. This involves pinpointing critical elements such as air conditioning units, heat pumps, and furnaces that demand regular maintenance. Recognizing the specific maintenance needs of these components is essential for crafting a checklist that aligns with your facility's operational profile.
Following the identification phase, adapt your checklist to match the specific demands of your facility. Take into account various factors, including the regional climate, which can significantly impact the maintenance frequency and types of tasks required. Facilities exposed to extreme weather conditions may necessitate more frequent inspections to ensure system resilience. Additionally, the scale of the facility and the intricacy of its HVAC infrastructure are pivotal in defining the maintenance approach. Larger facilities with complex systems might require more comprehensive checklists to ensure thorough coverage.
In customizing your checklist, prioritize tasks that mitigate the most prevalent issues encountered by your systems. For instance, in regions with high humidity, ensuring optimal coil cleanliness might be a primary concern to prevent mold growth. By structuring your checklist this way, you systematically address the most crucial maintenance activities, thereby boosting the overall performance and dependability of your HVAC systems. This methodical approach not only maximizes operational efficiency but also supports sustainable facility management practices.
Step 1: Conduct Seasonal Inspections
Scheduling seasonal inspections during transitional periods is crucial for ensuring your HVAC system is ready to meet the demands of peak seasons. These inspections should focus on assessing and fine-tuning system components to optimize performance and prevent potential disruptions. By addressing seasonal requirements proactively, facility managers can avoid unexpected breakdowns and enhance system resilience.
Begin by prioritizing components that are most susceptible to seasonal variations. As you prepare for the cooling months, emphasize tasks such as clearing debris around outdoor units, verifying refrigerant charge, and ensuring proper airflow in ductwork. When transitioning to the heating season, it is essential to inspect and clean burners, test safety controls, and ensure that heat exchangers are functioning without leaks or cracks.
To facilitate these inspections, a targeted seasonal HVAC maintenance checklist proves invaluable. It should include:
- Cooling Season Tasks: Focus on clearing condenser coils, validating refrigerant charges, and ensuring unobstructed airflow through ducts. These actions ensure efficient operation during hotter periods.
- Heating Season Tasks: Emphasize inspecting flue systems, testing burner assemblies, and confirming operational safety controls. These steps help maintain heating efficiency and safety standards.
Utilizing a seasonal checklist provides a thorough approach to maintaining system integrity and functionality. These regular inspections not only prevent potential issues but also contribute to long-term energy efficiency, supporting sustainable facility operations.
Step 2: Perform Regular Filter Changes
Regularly changing filters is vital to safeguarding the HVAC system's operational health and ensuring a clean indoor environment. Filters act as the first line of defense against dust, allergens, and pollutants, capturing these particles before they circulate through the facility. This preventive measure not only improves air quality but also helps the HVAC system function more efficiently by reducing unnecessary strain.
Set a routine to inspect, clean, or replace filters at least monthly, adapting to your facility's specific conditions. Ensuring filters are clear of debris prevents the system from working harder than necessary, thereby conserving energy and averting potential overheating issues. When air filters are clogged, the system's airflow is restricted, which can lead to increased energy consumption and potentially reduce the equipment's lifespan.
To optimize filter maintenance, consider the unique environment of your facility when determining the type of filters and their replacement frequency. Facilities in areas with higher pollution levels may need more frequent changes, while those with specialized requirements, like healthcare environments, might benefit from using HEPA filters for superior filtration. Tailoring your filter strategy to these specific needs ensures that the HVAC system operates efficiently, maintaining a healthy and comfortable atmosphere for everyone in the building.
Step 3: Check Electrical Connections
To maintain the reliability of your HVAC system, it's critical to focus on the system's electrical integrity. Over time, vibrations and environmental factors may loosen or damage electrical connections, potentially leading to inefficiencies or hazardous situations. Conducting regular inspections and securing connections can help prevent unexpected malfunctions and ensure optimal system performance.
During these evaluations, it’s essential to assess the system's electrical load by measuring voltage and current. This provides insights into any anomalies that might indicate issues such as circuit overloads or component degradation. Identifying these concerns early can avert severe damage and ensure continuous, efficient operation.
A methodical approach to inspecting electrical systems should include:
- Assess Wiring Condition: Closely examine wiring for signs of wear, such as cracks or exposed material, which can signal potential hazards requiring immediate remediation.
- Evaluate Electrical Load: Use diagnostic tools to check voltage and current levels. Ensuring these metrics align with manufacturer guidelines can reveal any operational discrepancies needing correction.
- Secure Connections: Regularly ensure all terminals are properly fastened to prevent electrical arcing or overheating, which can lead to system inefficiencies or failures.
By maintaining robust electrical systems, you not only protect the HVAC equipment but also uphold the overall safety and efficiency of your facility. This proactive approach minimizes downtime and supports the reliable operation of the building’s environmental control systems.
Step 4: Lubricate Moving Parts
Proactive lubrication of moving parts in HVAC systems is crucial for reducing friction and ensuring the equipment operates seamlessly. Without proper lubrication, friction can increase, leading to higher energy consumption and accelerated wear on components. By systematically applying lubricant, facility managers can enhance both the efficiency and reliability of their systems.
Start by identifying the components that require regular lubrication—such as fan motors, bearings, and moving joints. These elements are integral to the smooth operation of the HVAC system, and consistent lubrication helps maintain their performance. Adhering to the manufacturer's guidelines regarding lubricant type and application frequency is essential to avoid potential damage.
A structured lubrication strategy involves:
- Targeting Key Components: Focus on parts that endure significant movement and stress. Consistent lubrication helps them function efficiently without excess friction.
- Selecting Suitable Lubricants: Use the appropriate lubricant for each component to ensure compatibility and effectiveness in minimizing wear and energy use.
- Setting a Regular Schedule: Establish a consistent lubrication routine that aligns with the facility's operational demands. This practice prevents neglect and ensures optimal performance.
Incorporating regular lubrication into your maintenance routine actively supports the longevity of your HVAC system. This meticulous approach not only preserves the mechanical integrity of the system but also fosters a more sustainable and cost-effective facility management strategy.
Step 5: Inspect System Controls
A thorough examination of system controls is a key component in ensuring HVAC systems operate safely and efficiently. Controls dictate essential functions such as initiating operations and executing shutdowns. Any irregularities in these processes can lead to inefficiencies or even failures, making regular inspections critical to identifying and addressing issues before they escalate.
Start by meticulously evaluating the system's control settings. This involves confirming that the startup sequence progresses smoothly, with components activating in their designated order. Deviations from expected operations could signal underlying problems demanding immediate intervention. Moreover, ensure the shutdown process completes without abrupt halts, as these can cause unnecessary strain on system components.
A detailed control inspection should encompass:
- Calibration Verification: Ensure all control devices align with manufacturer specifications for accurate readings and responses.
- Safety Feature Testing: Verify that emergency shutdowns and safety interlocks function correctly to mitigate potential risks.
- System Feedback Analysis: Assess diagnostic data from control systems to identify any anomalies or error messages that may indicate issues.
Implementing these inspections as part of your maintenance schedule provides a comprehensive view of the system's performance and health. This approach not only optimizes system functionality but also upholds a secure and comfortable environment within the facility. Regular monitoring and timely interventions help ensure HVAC systems continue to operate effectively and reliably.
Step 6: Clean Coils and Components
Regular cleaning of HVAC coils and components is integral to ensuring the system operates efficiently and economically. Over time, evaporator and condenser coils can collect contaminants like dirt and grease, which can hinder airflow and reduce the unit's ability to regulate temperature effectively. Addressing this buildup not only enhances system performance but also optimizes energy usage, ultimately leading to cost savings.
Begin with the evaporator coils, which are crucial for absorbing indoor heat. These coils can become coated with grime, impairing their ability to cool effectively. Before cleaning, ensure the system is powered off for safety. Use a gentle cleaning agent designed for HVAC systems to loosen and remove deposits without damaging the fins, which are vital for heat absorption.
Next, inspect the condenser coils, typically located outdoors. These coils expel heat from the system, making their cleanliness essential for maintaining low operating temperatures. Clear any obstructions from around the unit to facilitate proper airflow. A low-pressure water jet can be used to wash away surface debris, while a specialized coil cleaner can tackle more ingrained dirt. Ensure thorough drying to avoid moisture-related issues before restarting the unit.
Additionally, evaluate other components such as drip pans and condensate drains. These can also become blocked over time, leading to potential water damage or system inefficiencies. Regularly clearing these components of buildup helps maintain system functionality and prevents moisture issues. This comprehensive maintenance strategy ensures that your HVAC system remains reliable and effective, delivering consistent comfort while maximizing efficiency.
Tips on Maximizing HVAC Efficiency
Enhancing HVAC efficiency requires strategic actions that not only optimize performance but also lead to significant energy savings. By integrating innovative practices, facility managers can ensure their systems operate smoothly, thereby reducing operational costs and promoting sustainability.
Optimize System Scheduling
To achieve efficient HVAC operations, implement a dynamic scheduling approach that aligns with the facility's occupancy patterns and external environmental conditions. This method ensures that energy is used judiciously, only when and where it is needed, without compromising comfort.
- Adaptive Timers: Use adaptive timers to adjust heating and cooling schedules based on peak and off-peak periods. This approach can significantly reduce unnecessary energy consumption during low-occupancy times.
- Demand Response Programs: Participate in demand response programs that adjust energy usage during peak demand times, helping to cut costs and improve grid stability.
Enhance Component Efficiency
Investing in high-efficiency components and ensuring they are maintained correctly can dramatically improve HVAC performance. This involves upgrading outdated parts and implementing technologies that enhance the system's overall efficacy.
- Variable Speed Drives: Install variable speed drives on motors and compressors to adjust energy use according to demand, preventing overconsumption and extending equipment life.
- Heat Recovery Systems: Utilize heat recovery systems to capture and reuse waste heat, improving energy efficiency and reducing operational costs.
Embrace Digital Innovations
Incorporating digital tools and technologies can provide deeper insights into HVAC operations, enabling more informed decision-making and proactive management. This digital transformation ensures facility managers can optimize their systems with precision.
- IoT Sensors: Deploy IoT sensors to monitor real-time environmental conditions and system performance, allowing for immediate adjustments and predictive insights.
- Cloud-Based Platforms: Utilize cloud-based platforms for data analysis and remote system management. These platforms provide actionable insights and facilitate efficient maintenance planning.
By leveraging these advanced strategies, facility managers can achieve significant improvements in HVAC efficiency, ensuring that their systems not only meet current demands but also contribute to a sustainable operational environment.
By following this comprehensive HVAC maintenance checklist and implementing the efficiency tips outlined, you can ensure that your facility's HVAC system operates at peak performance, providing a comfortable environment for occupants while minimizing energy waste and costs. However, managing these tasks can be complex and time-consuming, especially for larger facilities with intricate HVAC infrastructure. That's where we come in – our innovative CMMS solution is designed to simplify and streamline your HVAC maintenance processes, empowering you to work smarter, not harder. Schedule a Demo with us today and discover how our cutting-edge technology can transform the way you manage your facility's HVAC system.