Preventive Maintenance Checklists: A Complete Guide for Facilities, Schools, and More
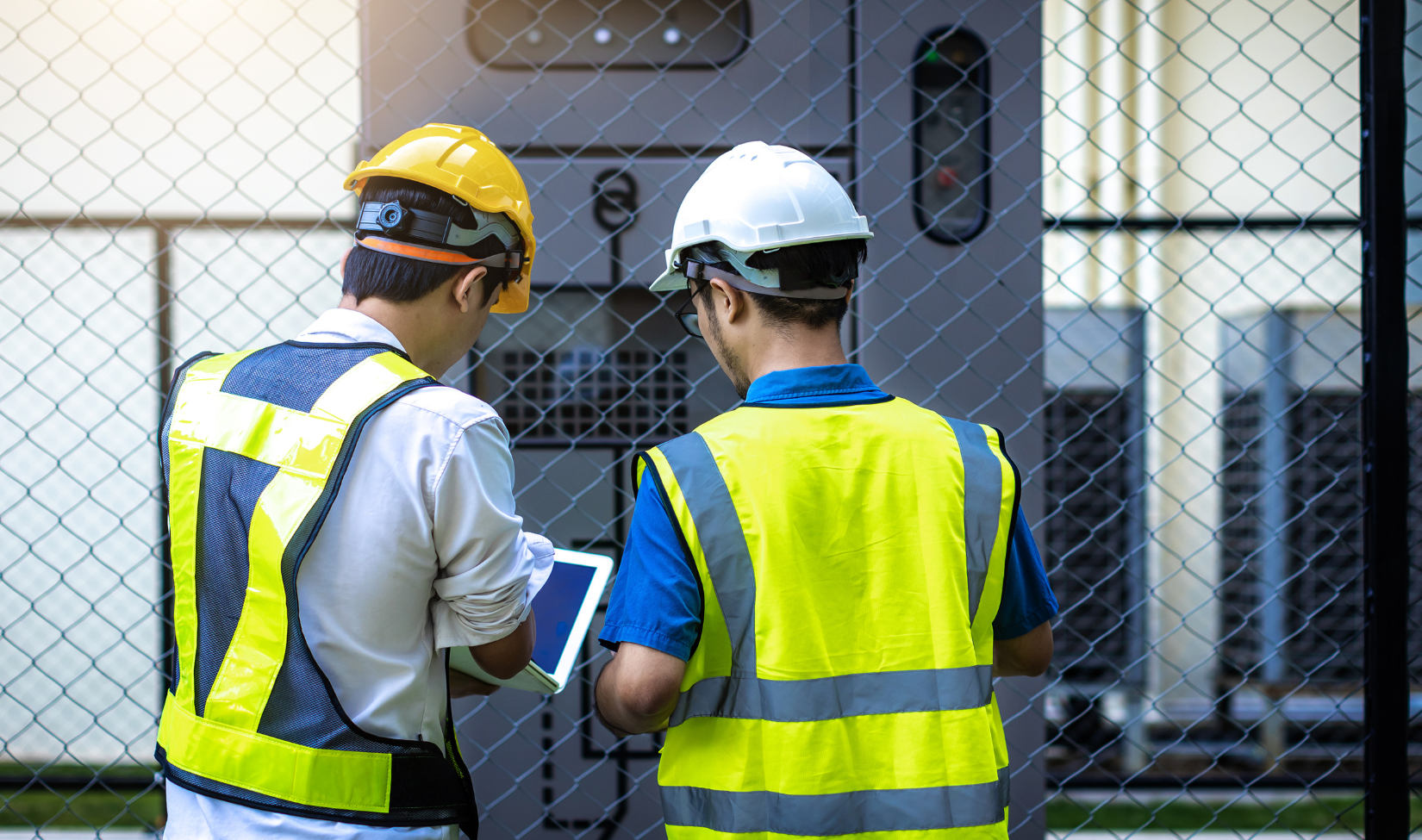
Preventive maintenance (PM) is the foundation of proactive facility management. Instead of reacting to breakdowns and equipment failures, preventive maintenance keeps your assets running smoothly with routine inspections, service, and upkeep. One of the most effective tools to streamline and standardize this process is a preventive maintenance checklist.
In this post, we'll walk through everything you need to know about preventive maintenance checklists—what they are, why they matter, how to build them, and how software like FlowPath can take your PM program to the next level.
What is Preventive Maintenance?
Preventive maintenance is regularly scheduled service and inspections designed to prevent equipment failure before it happens. It's the opposite of reactive maintenance, which happens after something breaks down. A strong PM program reduces downtime, extends asset life, improves safety, and saves money in the long run.
Schools, hospitals, municipalities, manufacturing plants, and commercial buildings all rely on PM to keep their operations running smoothly. Whether it's replacing HVAC filters every three months or inspecting a fleet of utility vehicles quarterly, preventive maintenance is all about consistency and planning ahead.
What is a Preventive Maintenance Checklist?
A preventive maintenance checklist is a standardized list of tasks that technicians and maintenance teams follow during routine inspections. It ensures nothing is missed, tasks are done consistently, and there's documentation of what work was completed.
Checklists are essential for organizing complex maintenance schedules across dozens (or hundreds) of assets for prime operational efficiency. They also provide a clear communication channel between teams and help new employees get up to speed quickly.
Benefits of Preventive Maintenance Checklists
- Improved Efficiency: Technicians know exactly what needs to be done, in what order, and how often.
- Standardization: Each preventive maintenance task is performed the same way across all assets and maintenance teams.
- Regulatory Compliance: PM checklists help ensure maintenance meets local, state, and federal compliance requirements.
- Equipment Longevity: Properly maintained equipment lasts longer and performs more reliably.
- Reduced Downtime: Prevent issues before they become emergencies.
- Cut Costs: By following a maintenance schedule, you can reduce the need for costly repairs and minimize maintenance costs by catching issues before they occur.
- Better Documentation: Track completed tasks, inspections, and repairs for auditing or warranty purposes.
How to Build Effective Preventive Maintenance Checklists
Creating an effective PM checklist requires more than just listing tasks for maintenance management. You need a strategy. Consider first what you want to accomplish with your checklists, who will be performing them, the scope of work possible, and the timing and cadence.
What You Need for Your PM Checklist
1. Define Service Intervals/Frequency: Weekly, monthly, quarterly, annually—define how often tasks are needed.
2. Determine the Inspection Process: Detail how to perform each inspection safely and thoroughly.
3. Create a Maintenance Plan: Define what needs to happen if something fails an inspection.
4. Start Record Keeping: Include space to log completed tasks, findings, and technician notes.
5. Maintain Parts Inventory: List any tools or replacement parts needed for service so you’re never delayed in your preventive maintenance plans by lack of supplies.
What Your Preventive Maintenance Checklist Should Cover
A complete preventive maintenance checklist should include:
- OEM Guidelines & Warranties: Follow manufacturer recommendations to avoid voiding warranties.
- Compliance Regulations: OSHA, EPA, state or municipal requirements.
- Internal Maintenance Goals: Reduce downtime, improve safety, stay within budget.
- Equipment Details: Serial numbers, location, manufacturer, install date.
- Visual Inspections: Check for damage, wear and tear, and hazards.
- Operational Checks: Test to confirm the asset is working properly.
- Maintenance Tasks: Cleaning, lubricating, replacing, adjusting.
- Safety Checks: Ensure all safety mechanisms and protocols are in place.
- Documentation: Who performed the work, when, and what was found.
Types of Preventive Maintenance Checklists
Your PM checklist should be tailored to the specific asset or system being maintained. Here are some common categories:
Building Systems
- Lighting: Inspect bulbs, fixtures, emergency lighting, and exterior lights.
- Safety Systems: Test fire alarms, extinguishers, AEDs, and emergency exits.
- HVAC: Replace filters, check refrigerant levels, inspect belts, and clean coils.
- Plumbing: Inspect for leaks, test water heaters, and clean drains.
- Building Interior: Inspect ceilings, flooring, door hardware, and wall integrity.
- Building Exterior: Check roofing, gutters, siding, walkways, and signage.
Equipment and Vehicles
- Fleet Vehicles: Oil changes, tire inspections, brake checks, fluid top-offs.
- Power Tools & Equipment: Inspect cords, test operation, clean filters.
- Utility Vehicles: Battery inspections, brake service, tire pressure.
- Material Handling Equipment: Forklifts, pallet jacks—check for hydraulic leaks, test controls.
Technology & Infrastructure
- Computers & IT Equipment: Clean vents, run diagnostic tests, check software updates.
- Network & Data Systems: Inspect servers, cable management, backup system checks.
- Electrical Systems: Inspect panels, test breakers, ensure grounding.
- Facility Infrastructure: Elevators, fire suppression systems, emergency generators.
- Aircraft (if applicable): Pre-flight inspections, fluid levels, component checks.
Preventive Maintenance Checklist Downloads & Examples
Free HVAC Monthly Preventive Maintenance Checklist
- Review equipment history and last service notes
- Gather required PPE and tools (gloves, safety glasses, filters, belt tool, multimeter, etc.)
- Follow lockout/tagout procedures before opening equipment
- Check general condition of unit (loose panels, rust, insulation damage)
- Look for oil stains around refrigerant lines (indicates leaks)
- Ensure drain lines are clear and pan is free of debris or standing water
- Verify no unusual vibrations or noise when unit is running
- Check access panels for secure closure and proper sealing
- Inspect and replace air filters (record size and date)
- Verify proper airflow at return and supply registers
- Look for dust buildup on vents or signs of airflow restriction
- Check thermostat or zone controller settings
- Inspect wiring for loose connections, frayed insulation, or corrosion
- Test system startup and shutdown sequence (confirm fan, cooling, and heating activate properly)
- Reset any overridden settings or manual modes in digital controls (if applicable)
- Visually inspect condenser coil for dirt and debris (clean if minor buildup)
- Check refrigerant line insulation for damage or wear
- Listen for unusual sounds from the compressor during operation
- Verify condenser fan is spinning freely and quietly
- Check for burner assembly cleanliness
- Test heating function from thermostat—ensure burner or heat strip activates
- Inspect flue stack or vent pipe for obstructions or corrosion
- Confirm access panels are reattached and secured
- Remove tools, debris, or old filters from jobsite
- Record findings, filter change dates, and any corrective action taken
- Note any issues for follow-up: parts to order, future repairs, deeper diagnostics
- Communicate key findings to facility manager or supervisor
Building Interior Preventive Maintenance Checklist
Monthly:
- Inspect hallways and common area floors for damage or trip hazards
- Check classroom and office doors for smooth operation and secure latching
- Look at ceilings and walls for water stains, cracks, or mold
- Test all restroom fixtures to make sure they work and drain properly
- Replace any burned-out light bulbs; test emergency lighting
- Make sure HVAC vents are not blocked or dusty
Quarterly:
- Tighten loose door hardware and lubricate squeaky hinges
- Deep clean high-traffic flooring like hallways and entrances
- Check restroom partitions for stability and secure hardware
- Make sure fire extinguishers are mounted correctly and inspection tags are current
- Touch up wall paint in high-traffic areas
- Inspect classroom furniture for damage or safety risks
Annual:
- Refinish gym floors or wax tile floors as needed
- Schedule full inspection of fire alarm systems by a certified vendor
- Replace stained or broken ceiling tiles
- Review and clean out storage areas; remove old or expired items
- Test classroom AV equipment, whiteboards, and mounted projectors
Building Envelope & Structure Preventive Maintenance Checklist
Quarterly:
- Inspect outside walls for cracks, staining, or signs of water damage
- Check all windows for cracked glass or broken seals; make sure they open and close smoothly
- Look at exterior doors and make sure weather stripping is in place and working
- Clean out gutters and downspouts; make sure water is draining correctly
- Inspect roof access ladders and hatches to make sure they’re safe and secure
Annual:
- Inspect the roof for damage, wear, or blocked drains
- Check the building foundation for cracks or signs of settling
- Re-caulk windows, doors, and any wall penetrations where needed
- Look at exposed steel or support structures for rust or weakening
- Inspect paint or exterior finish for peeling or sun damage
- Make sure roof drains and scuppers are draining water properly
Fleet Maintenance / Utility Vehicle Preventive Maintenance Checklist
Before Each Use
- Check fuel level
- Check tires for wear, damage, and proper inflation
- Verify headlights, brake lights, and turn signals are working
- Inspect for oil leaks or fluid puddles under vehicle
- Make sure seat belts (if present) are functional
- Confirm brakes are responsive during initial test
Monthly
- Check engine oil level and top off if needed
- Inspect air filter; clean or replace if dirty
- Test battery voltage and check connections for corrosion
- Lubricate steering and suspension points (if required)
- Inspect belts and hoses for cracks or wear
- Check coolant level in reservoir
- Clean exterior and interior; remove debris from bed or cargo area
Quarterly
- Change engine oil and filter
- Rotate tires if applicable
- Inspect drive components (chain, axle, shaft) for wear
- Check spark plugs and replace if needed
- Inspect brakes, pads, and rotors for wear
- Grease fittings (if applicable)
Annual
- Perform complete safety inspection
Replace air and fuel filters - Flush and replace coolant
- Perform load test on battery
- Review operator logs for any repeated issues
Safety Preventive Maintenance Checklist
Monthly
- Check all fire extinguishers for pressure, pin, and current inspection tag
- Test emergency lights and exit signs for proper function during power loss
- Ensure first aid kits are fully stocked and accessible
- Inspect eyewash stations for cleanliness, water pressure, and activation
- Make sure spill kits are stocked and properly labeled
- Confirm all safety signage is visible, accurate, and undamaged
- Inspect ladders and step stools for structural safety and secure footing
- Check AED devices for battery status and indicator lights
Quarterly
- Test building fire alarm system (manual pull stations, horns, strobes)
- Replace expired PPE items (gloves, masks, eye protection)
- Clean and lubricate eyewash stations and emergency showers
- Review and update emergency contact signage
- Inspect all safety guards on equipment and tools
- Check safety barriers, handrails, and floor markings for wear or damage
Annual
- Schedule full fire extinguisher inspection by certified vendor
- Perform evacuation drills and review safety plans
- Inspect confined space entry equipment (if applicable)
- Replace expired emergency kit materials (batteries, water, etc.
- Conduct full workplace hazard assessment walkthrough
- Provide safety refresher training for all staff
Create Digital Preventive Maintenance Checklists with FlowPath
If you're still using paper checklists or static Excel files to track preventive maintenance, you're not alone—but you're also missing out. Spreadsheets are a great starting point, but they come with limitations: no automatic reminders, no real-time updates, no easy assignment to your maintenance team, and no historical tracking unless someone manually inputs it. That’s where FlowPath comes in.
We’ve created free downloadable preventive maintenance checklists for schools and facilities to follow best practices—including HVAC, safety, utility vehicles, building interiors, and more. These editable spreadsheets are a great place to begin—but they’re even more powerful when used inside FlowPath.
- Upload them directly as attached checklist templates for assets
- Assign them as repeatable, scheduled work orders
- Track completions, technician notes, and missed tasks automatically
Want to go a step further? Use our built-in AI Assistant to customize the checklists to your equipment and facility needs, or automate PM scheduling by asset type or location.
FlowPath CMMS for Preventive Maintenance
FlowPath computerized maintenance management system is an all-in-one preventive maintenance software built to help facilities move from reactive to proactive maintenance with ease. With automated scheduling based on time, usage, or condition, FlowPath ensures your PM tasks are never missed.
With FlowPath, you can:
- Create custom PM templates for any asset or system
- Automatically assign each maintenance task to the right technician based on schedules
- Track service history and attach documentation
- Set alerts for upcoming or overdue maintenance
- Access everything from a mobile device—no clipboard needed
Our built-in AI Assistant helps generate and assign work orders, optimize plans, and predict future needs using real asset data. Teams can manage work orders, assets, and parts inventory in one system—complete with mobile access for technicians in the field.
From organizing maintenance schedules to tracking asset lifecycles and managing inventory, FlowPath facilities management software streamlines preventive maintenance from start to finish so you can move toward a predictive maintenance workflow.
PM Checklist FAQs
What industries need preventive maintenance?
Nearly every industry benefits from routine maintenance, including education, healthcare, manufacturing, government, and commercial real estate. Anywhere you rely on equipment, infrastructure, or vehicles—PM matters.
How often should preventative maintenance checklists be updated?
Review checklists at least annually or whenever equipment changes, OEM recommendations update, or compliance regulations shift.
What makes a great PM checklist?
Clarity, completeness, and relevance. A great preventative maintenance checklist is specific to the asset, easy to follow, and aligned with compliance and OEM requirements.
What are the benefits of preventative maintenance checklists?
They improve efficiency, reduce downtime, ensure safety, extend equipment life, and help your maintenance team stay organized and accountable.
How should tasks be prioritized on a PM checklist?
Use priority labels or categories (e.g., critical, high, medium, low) to focus on safety and compliance first, followed by performance and longevity. Find a cadence for regular maintenance that your team can keep up with to make the workflow manageable.
How can technology enhance PM maintenance?
Software like FlowPath enables automation, mobile access, documentation tracking, and easy scheduling—all of which streamline preventative maintenance and empower your maintenance team.