The Importance of Routine Maintenance When Managing Facilities
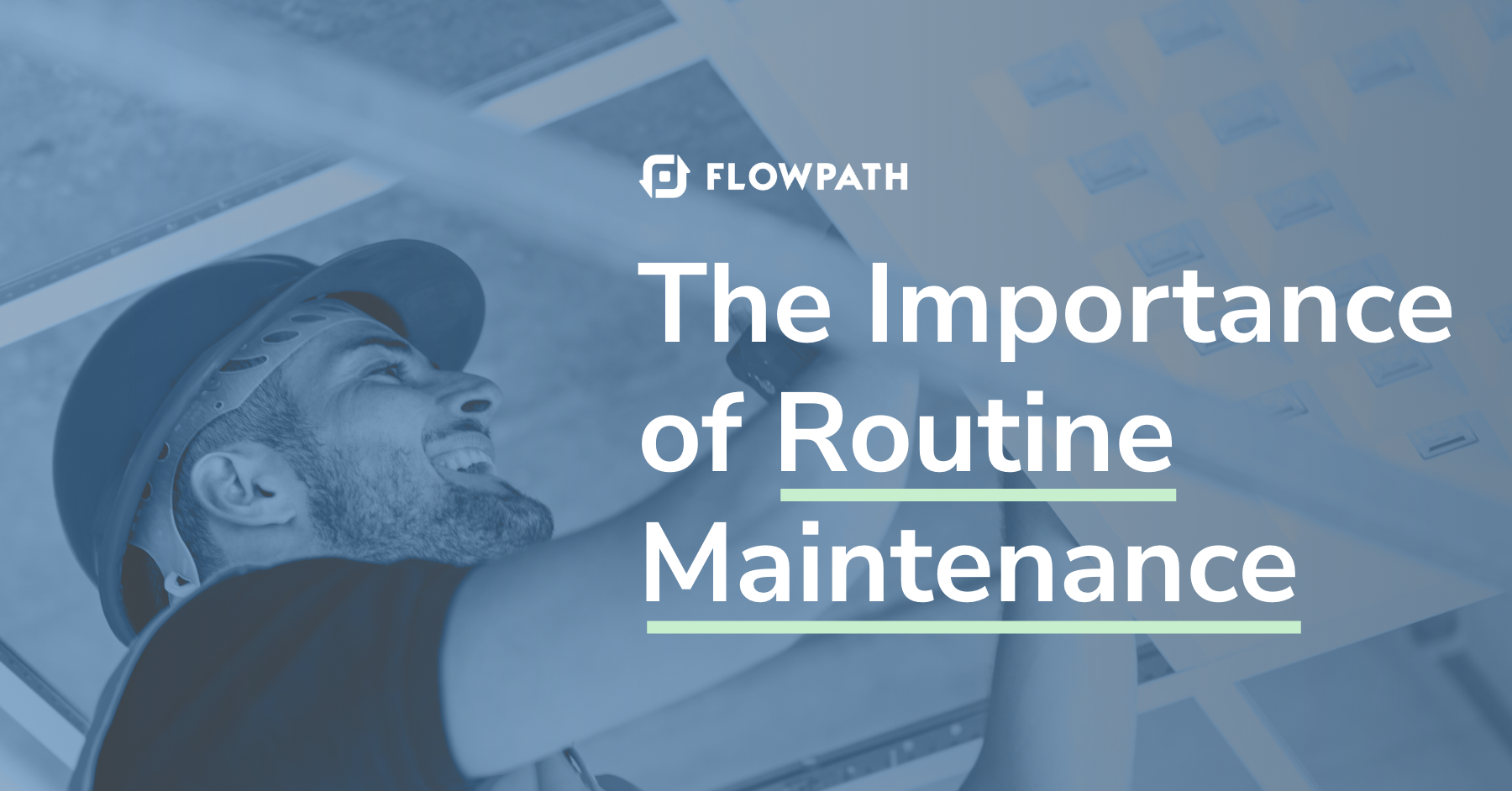
Routine maintenance is vital to the functionality of systems and facilities, but if it’s only being performed on an as-needed basis, problems can quickly arise. Equipment can break, production lines can be delayed, and workflows can be interrupted—all of which can rapidly add up. In fact, unplanned downtime caused by these inefficiencies can cost companies an estimated $50 billion annually.
Despite this astronomical cost, nearly 93% of companies admit that their maintenance processes are not very efficient. So, what’s the solution?
Enter: routine maintenance. By taking preventative measures, facility managers can mitigate or even avoid costly downtime, paving the way for improved performance, growth, and organization. Best of all, advancements in technology make managing maintenance-related tasks easier than ever. Read on to find out how to leverage and benefit from routine maintenance—and how FlowPath can help.
What is Routine Maintenance?
Routine maintenance includes any and all maintenance activities that are performed on a regular basis. These activities can include things like regular inspections, machine servicing, equipment checks, and more. Their main purpose is to catch any potential problems or issues before they snowball into a major disruption.
Routine maintenance is not unlike an annual exam at the doctor. These regular visits help set a baseline for health and allow health practitioners to catch and diagnose anything out of the ordinary with their patients. And, as with medicine, the earlier you detect a problem, oftentimes the easier it is to treat.
The Benefits of Routine Maintenance
Aside from catching problems early, there are several additional benefits to performing routine maintenance at every facility. Here’s the scoop:
- Reduce Emergency Work Orders: When things go significantly wrong, oftentimes an emergency work order is called in to save the day. This is especially important if a piece of equipment malfunctions and lives are at stake, but it can also be used in instances when threats to property and profits are in play. With routine maintenance, however, this type of work order can potentially be avoided—saving time, money, and people in the process.
- Improve Operational Performance: When something breaks—be it process or physical property—operational performance suffers. Timelines and deliverables get delayed, which can cause a ripple effect that’s ultimately felt by the end-user: the customer. Scheduling routine maintenance can majorly impact operations for the better, and could even mean the difference between staying on track and flying off the rails, so to speak.
- Facilitate Company Growth: It’s a well-known fact that operational delays are costly and can negatively impact the bottom line. Routine maintenance provides a notable return on investment, allowing those “emergency funds” to be more advantageously allocated toward growing the business.
While these benefits are undeniable, the act of managing routine maintenance might feel like another item on a never-ending to-do list. Luckily, there are modern-day solutions that make this process a breeze.
A Software Solution for Managing Routine Maintenance
Thanks to technological innovations, facility managers can schedule and manage routine maintenance with ease, freeing up valuable time to focus on big-picture tasks. Integrating software that assists with work order management can be a total game-changer—so much so that a whopping 80% of industrial maintenance companies link a CMMS to greater productivity.
For example, a common challenge that many facility owners face regarding routine maintenance involves finding reputable and consistent vendors to service their operations. What’s more, they often lack an efficient means of organizing the services of these vendors, defaulting to sticky notes, invoices, or even memory to keep track of work performed. FlowPath happens to be the only software on the market that can help alleviate this problem by organizing and integrating vendors in one place, making them easily accessible for routine maintenance needs.
Another real-world example of how FlowPath’s CMMS solves challenges around routine maintenance involves Meadowbrook Restaurants, an operator of multiple restaurant franchises. The business needed software with inventory management capabilities in order to scale their existing maintenance program, and FlowPath delivered. By connecting FlowPath with the facilities’ cloud-enabled freezer and refrigerator pressure sensors, Meadowbrook Restaurants can now automatically create work orders for preassigned technicians when something goes wrong. Ultimately, maintenance admin time was reduced by 70% with the help of FlowPath.
Read the full case study here >>
Here’s how FlowPath can help—even if you already perform routine maintenance.
Understanding and performing routine maintenance is the first step to alleviating costs and disruptions associated with equipment failure. The second step? Make it easy with FlowPath.
Integrating CMMS software that assists with assigning maintenance support is imperative for scalable growth, workflow organization, and even personnel performance. But with FlowPath, it’s not just about simplifying routine maintenance and automating work orders within a project; it’s about work order efficiency, plus project management planning and automation, calendar and event planning capabilities, and so much more.
Ready to find out how FlowPath can simplify the way facilities manage their operations and equipment? Schedule a demo to see our software in action and find out more about the benefits of our platform.