Unlocking Efficiency: Benefits of Predictive Maintenance in Operations
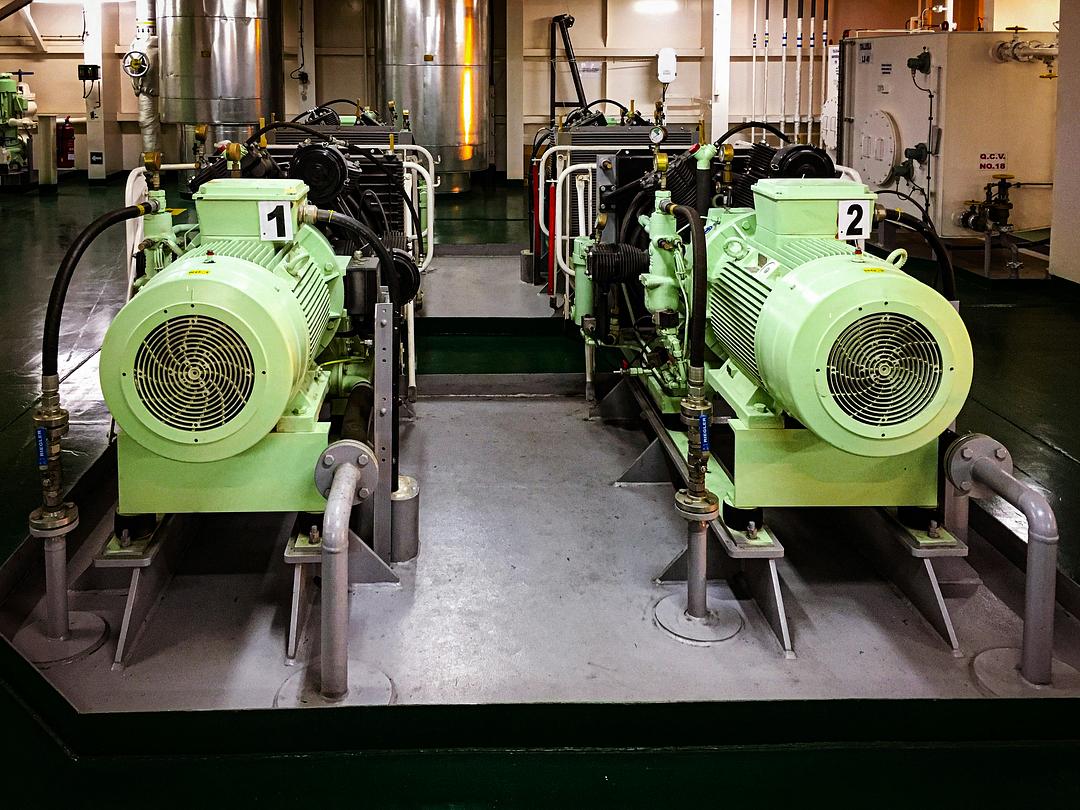
In today's fast-paced, technology-driven world, businesses are constantly seeking ways to optimize their operations and stay ahead of the competition. One strategy that has gained significant traction in recent years is predictive maintenance (PdM).
By leveraging advanced technologies and data-driven insights, PdM is revolutionizing the way organizations approach equipment maintenance and asset management. This proactive approach promises to deliver a wide range of benefits, from reducing downtime and minimizing costs to enhancing safety and improving overall operational efficiency.
As more and more companies recognize the potential of predictive maintenance, it's crucial to understand what it entails, how it works, and the key advantages it offers over traditional maintenance methods. In this article, we'll dive deep into the world of predictive maintenance, exploring its inner workings, real-world applications, and the transformative impact it can have on businesses across various industries.
What is Predictive Maintenance?
Predictive maintenance (PdM) is a data-driven strategy that focuses on maintaining the health of assets by analyzing and utilizing collected data intelligently. Rather than relying on fixed schedules, this approach determines when services and repairs should be performed based on an asset's failure to meet prescribed performance objectives.
PdM leverages a combination of sensors, IoT devices, and advanced analytics to continuously monitor equipment performance in real-time. By collecting and analyzing data on key parameters such as vibration, temperature, pressure, and more, PdM systems can identify subtle changes and anomalies that may indicate potential issues or impending failures.
The goal of predictive maintenance is to intervene at the optimal time—before equipment fails—thereby minimizing downtime, reducing maintenance costs, and extending asset lifespan. This proactive approach enables organizations to shift from a reactive "fix it when it breaks" mentality to a more strategic and efficient maintenance model.
How Predictive Maintenance Differs from Preventive Maintenance
While both predictive and preventive maintenance aim to keep assets running smoothly, they differ in their approach:
- Predictive Maintenance: PdM takes a proactive, data-driven approach. It leverages predictive technology to anticipate and prevent failures, thus reducing costs. Maintenance is performed based on the actual condition of the equipment, minimizing unnecessary interventions.
- Preventive Maintenance: Preventive maintenance follows a scheduled approach, with maintenance tasks performed at predetermined intervals based on time or usage. It relies on notifying software to alert caretakers about upcoming maintenance. While effective in reducing breakdowns, it may lead to over-maintenance and requires planned downtime.
By focusing on the actual condition of assets rather than arbitrary schedules, predictive maintenance enables more targeted and efficient maintenance activities. This approach helps organizations optimize resource allocation, reduce waste, and improve overall equipment effectiveness (OEE).
How Predictive Maintenance Works
Predictive maintenance hinges on a dynamic interplay of data acquisition and intelligent analysis, aimed at maximizing equipment reliability and performance. Central to this process are state-of-the-art sensors and IoT devices that capture a continuous stream of data on vital operational metrics such as temperature fluctuations, pressure variations, and equipment vibrations. This real-time data acts as a comprehensive diagnostic tool, providing insights into the current state of machinery and preempting potential issues.
Data Collection and Analysis: To deepen the insights derived from real-time monitoring, predictive maintenance systems integrate historical data, encompassing past maintenance records and detailed work order histories. This integration creates a robust dataset that enhances the predictive models used to forecast equipment behavior. Cutting-edge analytics paired with sophisticated machine learning models analyze this data pool, identifying patterns and predicting possible failure points long before they become critical.
Condition Monitoring and Fault Detection: These systems maintain an unbroken watch over equipment health, employing continuous surveillance to detect early signs of degradation or malfunction. When conditions deviate from the norm, predictive maintenance solutions swiftly issue alerts, enabling maintenance teams to act before minor issues escalate. This preemptive strategy not only averts unexpected machinery failures but also reduces the need for costly emergency repairs, ensuring that operations continue to run smoothly and efficiently. By addressing potential disruptions at their inception, organizations can sustain optimal asset performance and longevity.
Key Benefits of Predictive Maintenance
Predictive maintenance (PdM) offers a transformative set of advantages that fundamentally enhance operational capabilities. By leveraging data-driven insights, organizations can significantly reduce downtime and elevate efficiency levels across their operations. This approach not only minimizes unexpected production halts but also ensures that assets consistently perform at their peak. The proactive nature of PdM allows businesses to optimize preventive maintenance plans, thereby eliminating superfluous tasks and focusing resources where they are truly needed.
Reduced Downtime and Increased Efficiency: Predictive maintenance empowers organizations to anticipate and resolve equipment issues before they disrupt operations, thereby minimizing unexpected outages. This foresight ensures that machinery runs without interruption, boosting production schedules and overall efficiency. With a focus on timely interventions, businesses can streamline their maintenance efforts, directing resources to areas that most impact operational success.
Cost Savings and Extended Asset Lifespan: PdM facilitates strategic cost management by enabling targeted maintenance actions, thus avoiding the financial burden of emergency repairs. Early detection and resolution of potential problems help extend the longevity of vital assets, ensuring they deliver maximum return over their lifecycle. By refining maintenance expenditure and resource distribution, companies achieve financial prudence and enhance asset value.
Enhanced Safety and Compliance: In any operational environment, safeguarding personnel and equipment is critical. PdM plays an essential role in identifying and mitigating risks, reducing the likelihood of safety incidents before they occur. This proactive approach not only protects workers but also ensures adherence to regulatory standards and safety protocols. By maintaining equipment within safe operational parameters, organizations prevent severe failures that could endanger safety and disrupt compliance.
Implementing a Successful Predictive Maintenance Program
A successful predictive maintenance program hinges on a meticulous asset evaluation process, where assets are ranked by their importance to operational success and the potential consequences of their failure. This process involves an in-depth examination of each asset's role within the larger operational framework, ensuring that maintenance efforts are directed where they can have the most substantial effect. By focusing on assets that are critical to maintaining operational continuity, businesses can ensure that their predictive maintenance strategies are both effective and efficient. Analyzing past performance data is crucial in this phase; it provides valuable insights into recurring issues and helps identify key indicators of potential failure. Implementing the program in stages allows for a controlled rollout, starting with the assets that are most vital to operations and gradually expanding as the benefits become evident.
Investing in the right technology and expertise is crucial for the successful adoption of predictive maintenance. Organizations must choose sensors and IoT devices that are tailored to their specific operational needs, ensuring comprehensive data collection and analysis. The selection of predictive maintenance software is equally important; it should seamlessly integrate with existing operational systems to provide a unified data management solution. This integration is essential for transforming raw data into actionable insights that drive maintenance decisions. Equipping maintenance teams with the necessary skills and knowledge is also vital, as they need to interpret data effectively and execute maintenance tasks based on predictive insights.
Ongoing monitoring and optimization are key to sustaining the benefits of predictive maintenance. By regularly reviewing data insights, organizations can identify patterns and areas for enhancement. This continuous analysis enables the adjustment of maintenance strategies to reflect real-time asset conditions, ensuring that resources are allocated efficiently. Through an iterative process of refinement, businesses can maintain operational momentum and continually improve their predictive maintenance efforts, adapting to the changing needs of their facilities to maximize efficiency and performance.
The Future of Predictive Maintenance
Predictive maintenance is poised for transformation through breakthroughs in cognitive computing, enhanced algorithms, and smart connectivity. These cutting-edge developments will significantly bolster the capabilities of predictive maintenance tools, allowing them to process vast and complex datasets with unprecedented precision. As cognitive computing technologies mature, they will provide deeper insights into equipment behavior, while enhanced algorithms will facilitate adaptive learning and smarter decision-making. Smart connectivity, powered by a robust network of interconnected devices, will ensure seamless data flow and access to real-time information, enabling more targeted and effective maintenance interventions.
The advent of digital twins and augmented reality (AR) represents a paradigm shift in maintenance management. Digital twins provide a virtual representation of physical assets, offering a rich, real-time view of their status and performance. This digital counterpart allows for advanced simulations and scenario testing, enabling maintenance teams to optimize strategies without the risks associated with real-world trials. Augmented reality enhances this process by delivering interactive, real-time visualizations and instructions directly to technicians on site. This immersive technology ensures that maintenance personnel can conduct repairs and adjustments with greater accuracy and efficiency, minimizing downtime and resource expenditure.
In an increasingly competitive global market, predictive maintenance will be a cornerstone of strategic advantage. The foresight it provides into potential equipment issues will be essential for maintaining streamlined operations and reducing unnecessary expenditures. As industries face new challenges and opportunities, organizations that integrate predictive maintenance will be better prepared to navigate changes and capitalize on emerging trends. By embracing the latest technological advancements, predictive maintenance will empower businesses to enhance their operational performance, ensuring long-term resilience and growth.
As the landscape of facility management continues to evolve, predictive maintenance will undoubtedly play a pivotal role in shaping the future of operations. By harnessing the power of data, advanced analytics, and cutting-edge technologies, organizations can unlock new levels of efficiency, reliability, and performance. If you're ready to embark on your predictive maintenance journey and experience the transformative benefits it brings, we invite you to schedule a demo with us today and discover how our innovative solutions can revolutionize your operations.