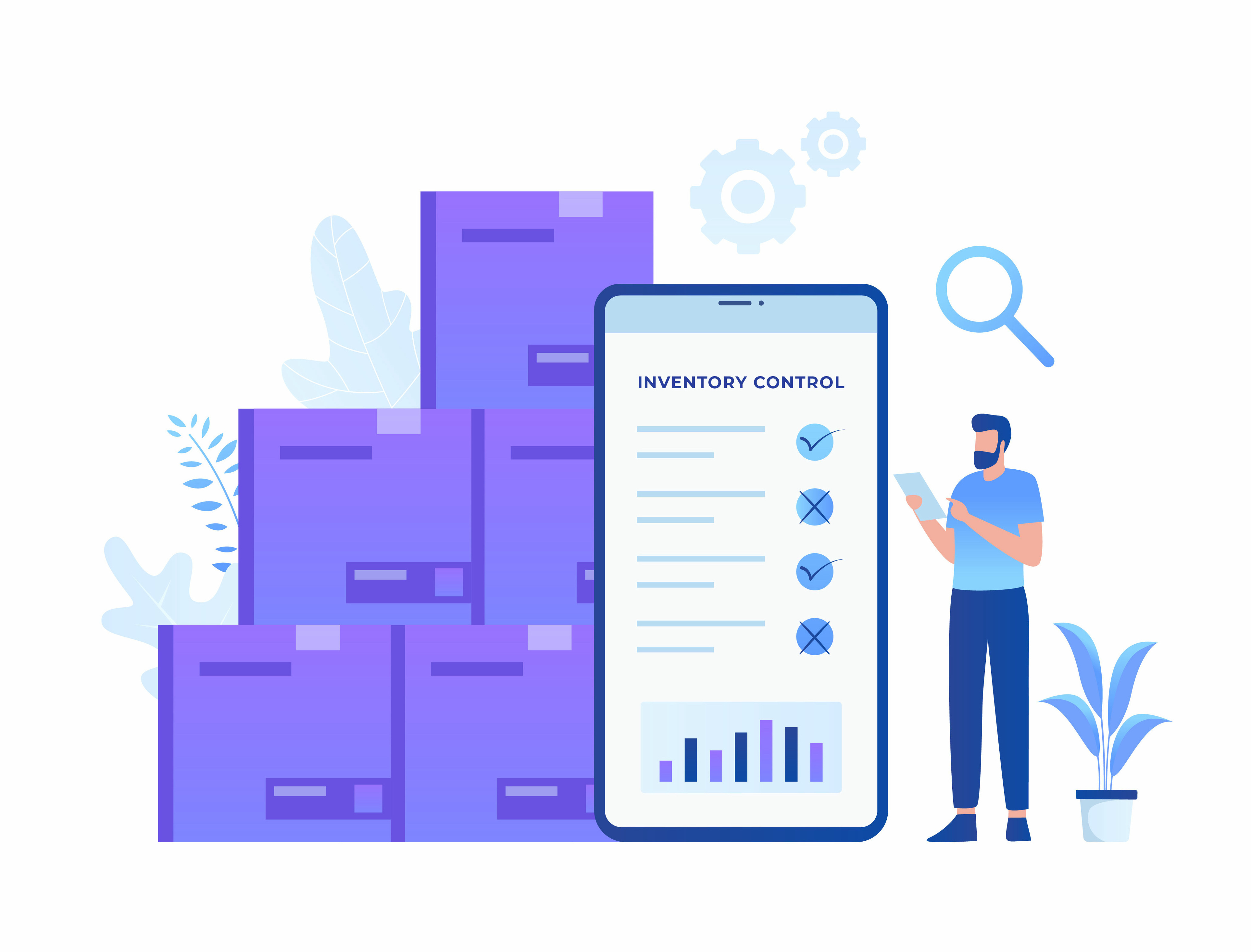
“Is my inventory management process doing enough for my facility?”
This is a common question many facility managers ask themselves often, especially when inventory gets out of hand and chaotic.
In this blog, we’ll be diving into the all-too-common scenarios of inventory management to see if it triggers your FM spidey senses.
Scenario 1: Improper Filing of Tasks
A routine work order just came in for your HVAC system that just turned itself off. Your technician used the last part to fix it two months ago and your supplier just ran out of the part due to supply chain issues. Scratching your head, you flip through your paperwork orders and see that the technician properly annotated using the part and noted that the parts inventory bin was now empty and more needed to be ordered. This note got lost in the pile of administrative work to be completed and now your building's internal environment is becoming untenable. Your phone rings and a very unhappy boss is on the other end wondering what is going on!
Unfortunately, this is a very common problem across the Facilities Management industry. Luckily, there are solutions to help your inventory management processes (and rid you of your current paper-based work order management!).
→ Solution: Audit Current Inventory Management Processes
The “supply chain” is taking the blame for a lot of parts inventory shortages these days. However, before allowing your company to put all the blame on suppliers, it’s worth taking a detailed look at your inventory management practices to ensure you are staying one step ahead of the supply chain in keeping your parts inventory bins stocked. The best Facilities Managers and Operations professionals know that a strong inventory management program is central to any successful organization.
How Do You Create an Effective Inventory Management Program?
For Facilities Managers, inventory management is comprised of procuring, systematically accounting for, and creating processes around expendable items routinely used for maintaining facilities. As a functional component of any good CMMS or CAFM system, inventory management needs to be integrated with other functional areas such as work orders, equipment, preventative maintenance, and reporting. Without this interwoven functionality, your inventory management process will be siloed and ineffective. Let’s explore why this is the case by digging into the inventory lifecycle, starting with procurement.
Best Practices When Procuring Inventory
Procuring inventory can be done in numerous ways, but generally speaking, it is where your organization interacts with vendors to supply you with materials and products.
Whether you use procurement software (for example, FlowPath integrates with Coupa) or run to Home Depot on an as-needed basis, you need to have a clear understanding of when it is that you need to procure items. If you are waiting too long, you will run out of parts and get yourself into a sticky situation, such as the one described in our example above.
If you are making recurring purchases without accounting for current inventory, then you are building up excess materials. In each case you are losing money with either stalled operations, underutilized headcount, or too much cash tied up in parts inventory. Identifying processes and workflows to help keep inventory numbers as accurate as possible will lead to increased success for your facility and its employees.
6 main features you need within a CMMS to be successful with Inventory Management
Smart purchase decisions start with strong inventory management. Following these best practices for the procurement of items you need to account for in inventory counts will be vital to know what your organization has on hand. A dedicated inventory management system that functions within a CMMS needs to have the following critical components:
- QR code generating system for easy scanning to receive, expend and identify parts
- Location-based storage tagging so you know where items are at all times
- Associating inventory to equipment and assets so there is no guessing which parts to use for certain fixes
- Simple adjustment reporting to match physical counts to what is in the CMMS
- Automated low-inventory alerts that prompt reordering of parts once on-hand count drops below a pre-determined threshold
- Ability to quickly add and expend parts to a work order for one-off purchases.
Scenario 2: How to determine how much to keep on shelves and when to reorder?
It should go without saying that any CMMS worth its salt should allow you to report on data collected within the system (check out how FlowPath does reporting here). Reporting allows you to create and monitor critical inventory management Key Performance Indicators (KPIs) that you can use to know how much to have in stock and thus, when to reorder.
With just two simple KPIs, you can begin to optimize your processes to free up cash, spend less money, execute your preventative maintenance without a hitch, and maximize operational uptime for the organization.
→ Solution: Identifying Important Inventory Management KPIs
- Meantime on hand - How long does a unique inventory item sit on the shelf on average before it is expended?
- Meantime to order - How long does it take on average to order the identified item?
When you are able to identify these two KPIs for parts, you can then plan out low inventory alerts, ordering schedules, and start to hold your organization accountable for any anomalies to the baseline. The meantime on hand tells you the frequency of use for a particular part, allowing you to draw out how many parts you would expect to use over a particular period of time. The meantime to order tells you the lead time needed to order a part before it hits your shelf.
Combine these two KPI’s and you now can figure out how to set your low inventory alert and optimize your inventory management practices. For example, if you find that you are using widget X every 3 weeks, but it takes the supplier 4 weeks to deliver widget X to your door, then you know you need to have at least two of these items on hand at all times.
Now, how many of widget X to keep on hand is an optimization conversation for another blog. However, standardizing the minimum amount on hand to allow for continuing operations for an acceptable period of time for your organization (should, say, a global pandemic rock the supply chain) is important. If in your risk management analysis you identify that you need a 3-months supply for ongoing operations, then the meantime on hand for each part will identify quantities for each part.
Take Inventory Management To the Next Level
A CMMS like FlowPath is the ideal solution. Our software is unlike any other facility management software out there because it does more and it does it better than the rest. From managing maintenance activities to project planning, team communication, and inventory management, FlowPath is the ultimate tool for facility managers looking to work more efficiently.