Reducing Emergency Maintenance with a Proactive Maintenance Approach
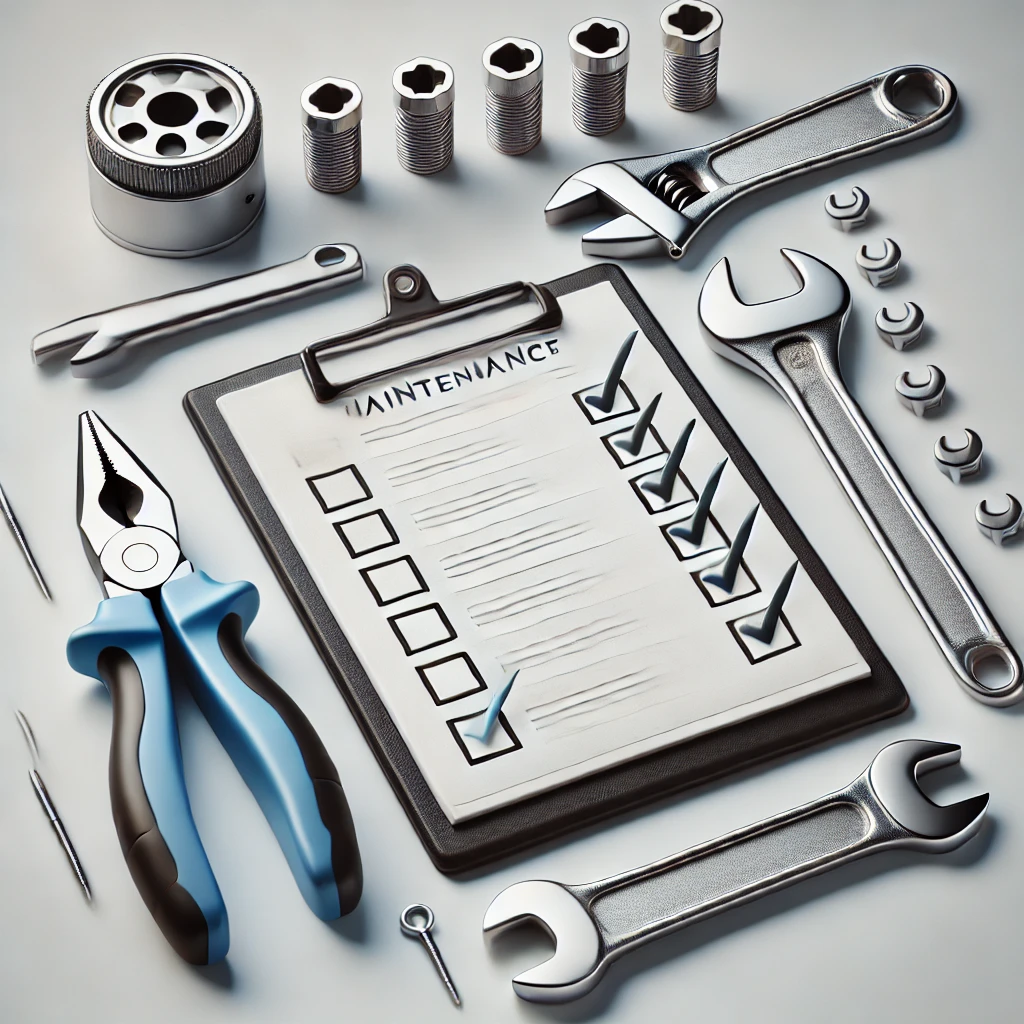
Introduction
Emergency maintenance is costly, disruptive, and often avoidable. By adopting a proactive maintenance approach, facility managers can mitigate the frequency of unexpected repairs, enhance asset longevity, and create a more stable operational environment. This article explores how proactive maintenance reduces emergency calls, controls costs, and supports seamless facility operations.
For more insights on proactive facility management, check out these FlowPath resources:
- Emergency Maintenance: How to Manage and Reduce It
- Proactive Maintenance with FlowPath’s AI Assistant
- How to Master Maintenance Schedules
The Cost of Emergency Maintenance goes beyond the price of repairs. Emergency repairs often require specialized labor, rush shipments for replacement parts, and after-hours services—all of which drive up costs. Moreover, emergency maintenance can disrupt workflow and productivity as employees must halt regular tasks to address urgent repairs. By adopting a proactive approach, facility managers can avoid these reactive costs, streamline repair processes, and focus resources on scheduled maintenance, which is often more economical and less disruptive.
A proactive maintenance strategy leverages scheduled inspections and data analysis to address issues before they escalate into emergencies. Regularly scheduled maintenance allows facility managers to detect early signs of wear or damage that might lead to breakdowns. For example, checking HVAC filters monthly can prevent airflow issues that could cause a system shutdown. In a proactive approach, maintenance tasks are anticipated and performed on a routine basis, minimizing surprise repairs and maintaining smooth operations.
Leveraging technology in proactive maintenance is another critical component. CMMS systems like FlowPath enable facility managers to monitor asset performance through real-time data and predictive analytics. With these tools, managers gain insight into equipment usage patterns, potential failure points, and operational trends, allowing for more strategic maintenance planning. By integrating data-driven insights into the maintenance process, managers can anticipate issues and take preemptive action, extending asset lifespans and preventing unexpected failures.
Reducing Downtime through Predictive Insights enhances operational efficiency and reliability. When maintenance is planned and executed in advance, there is less risk of equipment failure during critical operational hours. Predictive insights allow facility managers to prioritize high-risk assets for regular checks, ensuring that the most essential equipment remains functional and reducing downtime. This not only improves productivity but also enhances service quality by ensuring that facility operations remain uninterrupted.
Improving Resource Allocation and Staff Efficiency is a significant benefit of proactive maintenance. In a reactive maintenance model, teams are often pulled from planned tasks to respond to emergencies, disrupting workflow and stretching resources thin. A proactive model allows facility managers to allocate resources more effectively, scheduling maintenance when it’s convenient and minimizing the need for emergency call-outs. Staff can focus on their designated tasks, knowing that unexpected breakdowns are less likely to derail their workflow.
Enhancing Safety and Compliance through proactive maintenance is crucial, especially in facilities where equipment failures could endanger staff or occupants. Regular inspections ensure that equipment remains safe and compliant with regulatory standards, reducing liability and creating a safer environment. Proactive maintenance helps prevent hazardous breakdowns, making it easier to uphold safety standards and protecting the facility from potential compliance issues.
Conclusion
A proactive maintenance approach not only reduces emergency repairs but also provides cost control, operational reliability, and enhanced safety. By leveraging technology, scheduled upkeep, and predictive insights, facility managers can mitigate disruptions and create a more resilient facility environment. To explore how FlowPath’s CMMS can support your proactive maintenance strategy, read our guide on Proactive Maintenance with FlowPath’s AI Assistant.
Ready to reduce emergency repairs and improve facility efficiency? Schedule a Demo with FlowPath to learn how our CMMS can support a proactive maintenance approach for your facility.